曲げ金型段取りの自動化
による絶大な効果
曲げ加工に変革をもたらす「ATC」
かつて板金の曲げ加工は「スキルが求められる作業」とされていて、伸びや曲げ順などを熟知したベテランが担当していました。
近年の曲げ加工の作業は、曲げ加工機の高機能化、金型の高精度化、曲げ加工用プログラム装置の進歩により、徐々に専門知識を持たない人も担当できる加工となってきました。
この流れをさらに加速させているのが、金型自動交換装置(ATC)付きの曲げ加工機の登場です。
そこで、金型自動交換装置付き曲げ加工機「HG-ATC」を導入に至った会社の背景とその運用についてご紹介します。
ここで紹介する4社は、いずれも「多品種少量生産」という生産形態では共通しています。その一方、製品は「新規品」中心か「リピート品」中心か、担当者は「ベテラン」か「経験の浅い社員」かなど、企業によって運用のしかたにバリエーションがあるのがポイントです。
熟練工不足の中で「誰でも即戦力」に
(株)フジサキ(愛媛県伊予市、藤崎文吾社長)の場合、曲げのベテラン作業者が突然退職したことが「HG-1003ATC」導入の直接的なきっかけになりました。
当時、同社の社員は総勢7名で、曲げ工程の設備は「RG」のみ。金型選定から金型レイアウト、曲げ順序の検討まで、すべて現場の職人に任せていました。そうした状況下での主力メンバーの離脱は、きわめて大きな痛手でした。大至急、曲げ作業者を確保する必要がありましたが、即戦力の経験者を見つけるのは容易ではありません。
藤崎社長は「スキルを持たない社員を1日でも早く戦力化しなければなりませんでした。しかし、曲げ作業は段取りが難しい。当時の設備はRGだけで曲げのCAMもなかったので、なおさらです。新しく担当する社員に曲げのノウハウを伝え、育てるには多くの時間がかかります。とても待てません」。
「HG-ATCは、こうした人材の課題を解決でき、経験の浅い社員でも曲げ加工ができるようになると考えて導入を決めました。CAM(VPSS 3i BEND)の完成度も高く、すぐに成果が出るだろうと見込んでいました」と語っています。
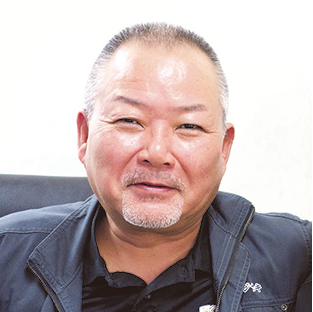
藤崎文吾社長
「HG-ATCの導入当初は工場長に任せてマシンの性能を把握してもらい、その後は20代の経験の浅い社員に担当してもらいました。この若手社員は、材料や表面処理の種類がある程度わかっているくらいの知識量でしたが、HG-ATCをフル稼働できるようになるまで1カ月もかかりませんでした。その次は、複合マシン(LC-C1NT)のオペレーターがHG-ATCとの2台持ちで曲げ加工も行うようになりました」。
「HG-ATCであれば、少し教えるだけですぐに戦力になってくれる安心感があります。社員を教育するコストと時間を大幅に減らせるので、費用対効果は十分です。今後も配置換えをしながら曲げ加工ができるメンバーを増やしていく予定です」(藤崎社長)。
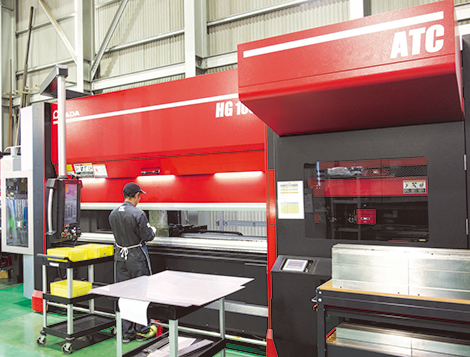
HG-1003ATC
外国人スタッフを早期戦力化
田中産業(株)(静岡県三島市、田中公典社長)は、ベトナム人スタッフが全体の50%前後を占めるダイバーシティ工場です。「HG-1003ATC」を導入した当時は、社員63名のうち半数以上がベトナム人。そのうち6割が高度人材(エンジニア)で、4割が技能実習生・特定技能という内訳でした。
田中社長は「ベトナム人スタッフに曲げ加工を任せようとしたとき、スキルが必要な金型段取りの作業を自動化し、教育コストを削減できるHG-ATCが最適と考えました。技能検定の取得支援制度などを整備して人材育成にも力を入れていますが、働き方改革で残業時間が制限される中、生産量を増やしながら外国人スタッフの教育もしていくのは大きな負担でした」と語っています。
「HG-ATCを導入してから1カ月もかからずに、未経験のベトナム人スタッフが曲げ作業をできるようになりました。金型交換を自動化できたことだけでなく、NC端末(AMNC 3i)の操作性が優れているのも大きかったと思います。AMNC 3iは曲げ形状や曲げ順序の表示がわかりやすく、NC端末との対話で加工を進められるので、ベトナム人スタッフにとっても扱いやすかったようです」。
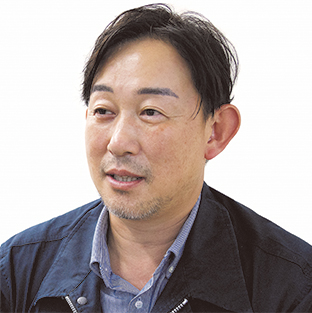
田中公典社長
「HG-ATCをメインで担当していたベトナム人スタッフが急きょ、体調不良で入院してしまったことがありました。入院している間は、少しだけ曲げの経験がある別のベトナム人スタッフに担当してもらいました。本来ならかなり動揺する場面だと思いますが、配置を変更した初日からスムーズに稼働できたのは驚きでした。こうしたアクシデントが発生しても納期遅れや不良発生といった悪影響がなく、生産を続けられるのは、会社にとって本当にありがたかった」(田中社長)。
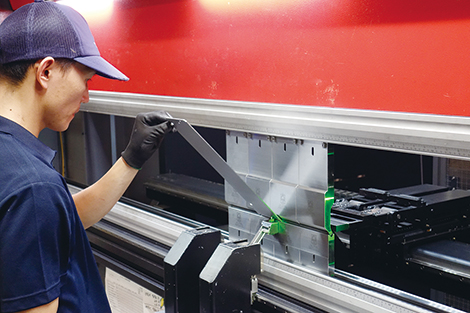
HG-ATCは高度外国人材が担当
「多品種少量生産」に絶大な効果
金型段取りの自動化ソリューションは、「多品種少量」の生産形態で大きな効果を発揮します。
単純な原価計算では、「段取り時間」を「生産ロット数」で割ったものが「製品1個あたりの段取り工数」になります。「段取り時間」が30分だった場合、ロット10個であれば「製品1個あたりの段取り工数」は3分、ロット100個であれば18秒になります。ロットが大きい量産品では目立たなかった「段取り時間」も、多品種少量生産では工場の生産能力やコスト競争力に大きく影響することになります。
(株)佐藤電機製作所(工場:山梨県山梨市、佐藤薫宏社長)の場合、「多品種少量生産へのシフトが進んできたこと」が「HG-ATC」導入の大きな理由でした。
同社は大手電機メーカーとの取引が長く、ロットサイズは最大2,000個と「量産」が中心の生産形態でした。しかし、数年前からこの得意先の生産量が減り、新たに医療機器や半導体製造装置などの仕事を取り込んでいったことで、「多品種少量生産」の仕事が増えてきました。
佐藤社長は「曲げ工程は段取り工数が目に見えて増え、ボトルネックになっていたため、金型段取りを自動化できる「HG-1003ATC」の導入に踏み切りました。ただ、すべての製品が多品種少量というわけではないため、曲げ工程全体、工場全体を最適化するためのカードのひとつという認識です」と語っています。
同社の曲げ工程は、自動金型段取りが可能な「HG-1003ATC」、コンパクトな「EG-6013」、オールラウンドな「HDS-1303NT」の3機種が主力で、それぞれの特性を考慮した使い分けを行っています。
「HG-ATC」で主に加工しているのは、金型段取りの回数が多くなる「小ロット」の製品や、曲げ工程数が多い「複雑形状」の製品。対照的に、「EG」では「単純形状」でロットが大きい「量産」の製品。「HDS」ではサイズが大きい製品(~3m)や加圧能力(~130トン)が必要な製品を中心に加工しています。
主力ベンディングマシン3機種の稼働分析
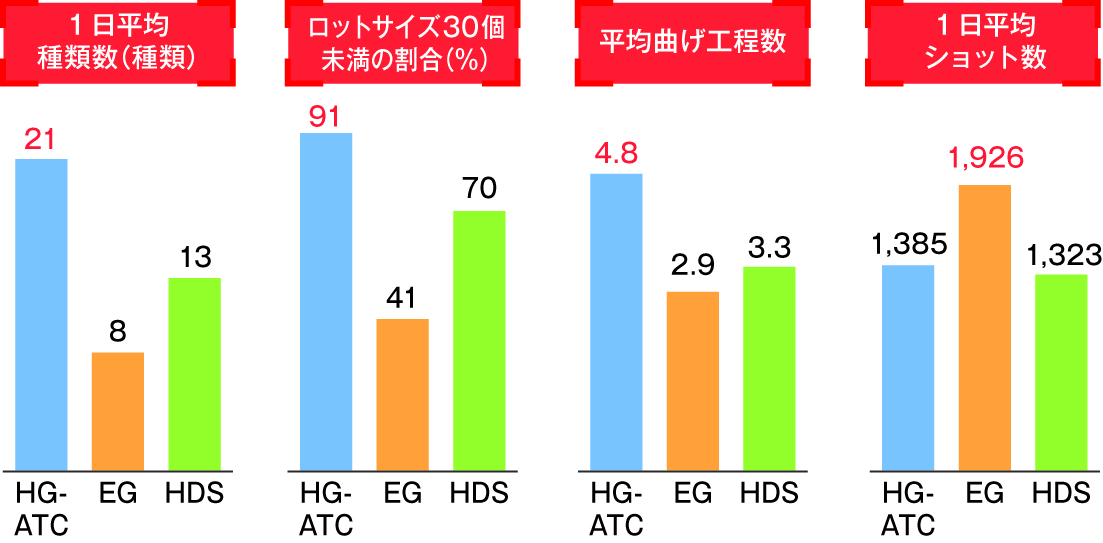
佐藤社長は「多品種少量・複雑形状の製品の場合、RGのような旧式のマシンと比較すると3~3.5台分の仕事をこなしてくれます。こうした『手間のかかる製品』をHG-ATCが引き受けることで、ほかのマシンの負荷が減り、スムーズに生産できるようになりました。HG-ATC単体の効果というよりもこの相乗効果が大きく、曲げ工程全体の生産性は20~30%改善したと思います」と語っています。
佐藤社長は2016年に導入した1台目の「HG-ATC」の効果が大きかったことから、「多品種少量生産へのシフトは今後ますます加速していきます。HG-ATCを増設して多品種少量生産への対応力を強化し、対応できる板厚の幅を広げていきたい」と語っており、2021年には2台目を、2022年2月には3台目を導入しました。
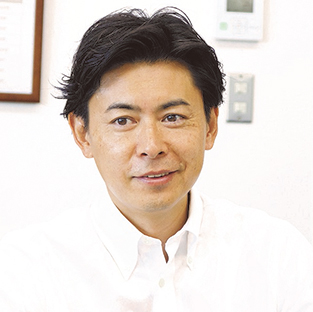
佐藤薫宏社長
「多品目一括金型段取り」で
段取り削減
「HG-ATC」と曲げ加工用CAMの「VPSS 3i BEND」の特徴的な機能として「多品目一括金型段取り」があります。これは「HG-ATC」の分割金型の特性を生かし、「多品目」(板厚ちがいを含む複数の製品)の曲げ加工に対応する金型レイアウトを自動作成する機能で、金型段取りの回数そのものを大幅に減らす効果があります。
ここで紹介する2社は、いずれも多品目一括金型段取りによって大きな成果を挙げています。「新規品」中心、「リピート品」中心というちがいはありますが、両社とも、ブランク工程ではオーダー単位・機種単位で部品をまとめて割り付ける「ファミリーネスティング」を行い、そのまま機種ごとのまとまりで溶接組立工程まで流していく「アセンブリー生産」の方式を採用しています。
先にご紹介した(株)フジサキは、主に「新規品」の多品種少量生産で成果を挙げています。
たとえば、同社が手がける自動省力化産業機械の仕事は、1機種につき150点前後の板金部品で構成されます。すべて新規品で、ロットはほとんど1~2個。溶接組立まで行ってから出荷します。
ブランク工程はファミリーネスティングで、基本的には得意先・案件のまとまりでシートに割り付けます。ブランク加工が完了したものから曲げ工程へ受け渡すため、同じ板厚ではあるものの様々な形状の製品が1~2個ずつ、流れてくることになります。
「HG-ATCを導入するまでは、きつい仕事でした」と藤崎社長は振り返ります。
「以前は、1回の金型段取りでまとめて加工できる製品を作業者が見極め、仕分けていました。この見極めができる作業者は限られますし、仕分けにかかった時間だけ曲げの稼働率は下がります。作業者のスキルによって所要時間・品質のバラツキが出てしまうのも悩みでした」。
「HG-ATCと多品目一括金型段取りを活用するようになってからは、まず金型段取りの回数自体が減り、さらに加工する製品の見極めと仕分けが不要になったことで段取り作業の時間が大幅に短縮できました。多品目一括金型段取りを使えば、作業者のスキルに左右されることなく、金型段取りの回数を大幅に減らすことができます。1つの機種の構成部品が100品目あったとすると、段取り回数は20回くらいになるイメージです。使わないともったいない機能だと思います。当社では100%、使用しています」(藤崎社長)。
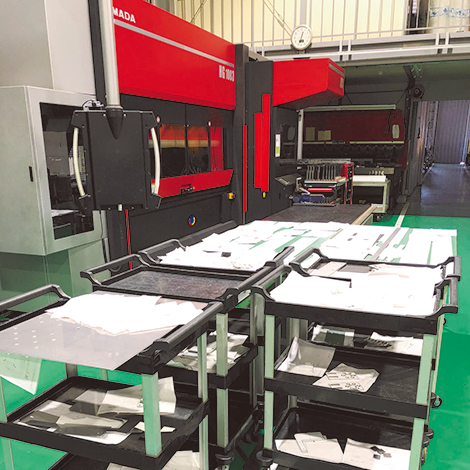
多品目一括金型段取りを100%使用
工場全体の生産性が30%改善
(株)内田製作所(神奈川県厚木市、内田健一郎社長)は、「リピート品」中心の「アセンブリー生産」で多品目一括金型段取りを活用しています。
「HG-ATC」で主に加工しているのは、曲げ工程数が比較的多い(5~6工程)工作機械カバーや半導体製造装置関連の製品です。これらの製品は、一度仕様が決まると大きく変わることはなく、数週間~1カ月置きのペースで同じ製品をリピート受注しています。以前はその都度、加工する製品の選定や金型段取りを行っていましたが、ブランク工程の処理速度に曲げ工程が追いつかず、曲げ待ちの仕掛り品が積み上がっていました。
内田社長は、「HG-ATC」を導入した理由として「ボトルネックになっている曲げ工程の流れをスムーズにしたかった」と語っています。
「HG-ATCの担当者にはベテラン社員を配置し、運用方法について試行錯誤を重ねました。現在の運用方法は、リピート率の高さを生かし、多品目一括金型段取りを使って機種単位の構成部品の加工データをつくり込んでおき、リピート受注のたびにそれを呼び出して加工するというものです」。
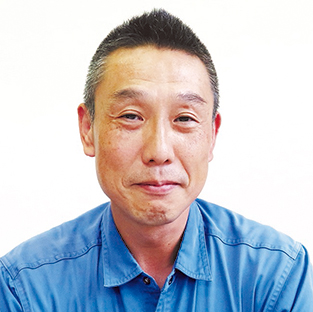
内田健一郎社長
「加工データをつくり込む生産準備の段階では、HG-ATCで加工する製品の選定やグループ分けにスキルとノウハウが必要になりますが、加工データができてしまえば、作業者は迷うことなく1回の段取りで何十品目も加工できます。1機種あたりの構成部品は数十点で、小さなブラケットから大きなカバーまでさまざまです。板厚ちがいの製品も含まれるため、V幅のちがう金型を同時に並べるパターンもあります。これまで金型段取りが20~30回必要だったのが、6回くらいでまかなえるようになった機種もあります」。
「加工品目数は1日平均50品目。従来機と比べて2倍以上に増えています。ブランク工程から溶接組立工程まで一気通貫でスムーズに流せるようになり、工場全体の生産性は30%程度改善しました。段取りの回数や考える時間が減った分だけ稼働率が改善し、山積みになっていた曲げ待ちの仕掛り品はほぼ解消しました」(内田社長)。
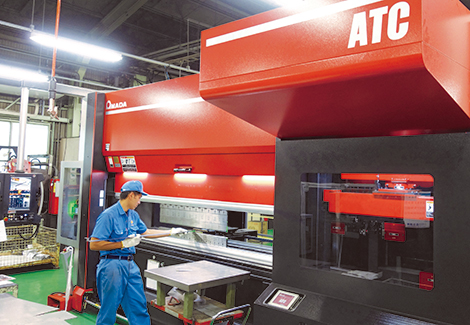
多品目一括金型段取りを積極活用
「もしもHG-ATCがなかったら?」
最後に、「もしもHG-ATCがなかったら?」という質問に対する各社の回答を紹介します。
「そんな状況は想像もしたくありません。もしかしたら、今も私が現場に入って、RGで曲げていたかもしれません。不良も増えるでしょうし、社員も『まちがえてはいけない』というストレスを感じながら仕事をしていたと思います。人手不足や働き方改革に対応するためにも、HG-ATCは必要不可欠な設備です」(フジサキ・藤崎社長)。
「HG-ATCはなくてはならない存在です。担当者が病気で離脱したときなどは、現場が相当混乱していた可能性があります。ATCやロボットにより自動化が進んでいけば、曲げ工程は従来のようなボトルネック工程ではなくなっていくと思います」(田中産業・田中社長)。
「HG-ATCがなかったら、協力工場に頼らなくては生産量を維持できず、収益性も落ちていたと思います。また、工場視察にいらっしゃったお客さまのHG-ATCに対する印象は非常に良い。こうした広告効果も得られなかったと思います」(佐藤電機製作所・佐藤社長)。
「今の仕事量はとてもこなしきれなかったでしょう。もともと曲げ工程がボトルネックになっていたので、納期遅れを頻発し、お客さまの信頼を失う負の循環に陥っていたと思います。そうならないためには残業で踏ん張るしかありませんが、当時はすでに社員がギブアップ寸前でしたから、会社全体がおかしくなっていた可能性もあります」(内田製作所・内田社長)。
「HG-ATC」は立ち上がりがスムーズで、運用が軌道に乗るのが早いという評価も多く聞かれます。また、検討段階で導入効果に懐疑的だった企業も、1台目を導入してからは「もっと早く入れておけば良かった」と、2台目、3台目を続けて導入していくパターンも増えています。
金型段取りの自動化ソリューションは、「人手不足」や「多品種少量生産」への対応が課題となっている板金工場にとっては高確率で、「アセンブリー生産」を採用している場合はより大きな効果が期待できるといえるでしょう。
記事:マシニスト出版