ファイバーレーザ溶接で
工数90%短縮を実現
重要度が高まる溶接工程
近年の板金加工では、デザイン性の高いカバーが増えるとともに、外観への要求が高まってきています。
その典型的な例として、かつてはスポット溶接による接合で表面にスポット痕が残っていた鉄道車両をはじめ、様々な製品からスポット痕が見られなくなってきました。
このように、板金加工の溶接工程は、薄い板材でカバーや機構部品などを製作するうえで、強度や精度だけではなく美観など、製品の品質を左右するとても重要な工程となっています。
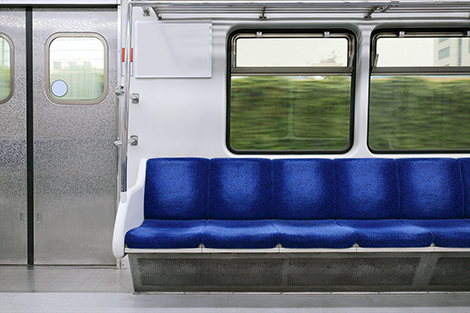
技能者不足が喫緊の課題
多くを要求される溶接作業は、高度なスキルが必要になり、技能取得に長い年月がかかる難しい技能です。
一般社団法人日本溶接協会によると溶接技能認定者は全体では23万人程度で横ばいですが、炭素鋼を対象とする手溶接は年々減少傾向となっており、技能者の育成が喫緊の課題となっています。
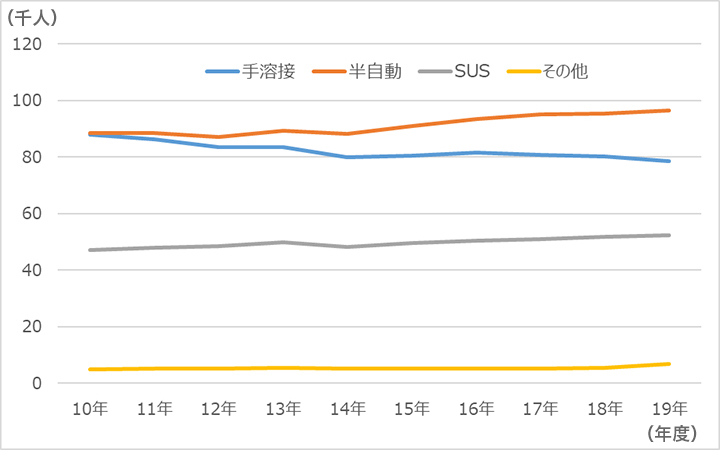
出典:一般社団法人日本溶接協会
溶接により生じる製品の熱ひずみも大きな課題です。
前述のように外観が重視されひずみに対する基準も厳しくなっています。
これに対し、ひずみ取りはまさに勘と経験の世界で、熟練者ですら多くの時間を要する難易度の高い作業です。
入熱を最小に抑えるレーザ溶接
このように熟練の技能を必要とする溶接と仕上げ作業に変革をもたらすのがレーザ溶接です。
レーザ溶接は、文字通りレーザ光を熱源に材料を溶かして接合する方法です。
TIG溶接やMAG溶接などのアーク溶接は、トーチ(電極)から放電したアークを熱源とし材料を溶かして接合する方法で、アークの広がりとともに加熱される範囲が広くなるため、焼けやひずみなどの熱影響が大きくなってしまいます。
これに対してレーザ溶接は、スポット径が直径1mm未満の極小径のレーザ光で溶接するため、材料への入熱を少なくし、焼けやひずみを抑えることができます。
下図は、SUS304 板厚1.5mmの製品をTIG溶接、ファイバーレーザ溶接それぞれで行った際の製品のひずみ量を測定した比較データです。
TIG溶接では
最大3.01mmひずんでいましたが、ファイバーレーザ溶接では 最大0.638mmでひずみ量がTIG溶接比で79%減少し、熱影響の少なさがひずみを抑えることが分かります。
溶接方法によるひずみ量の比較
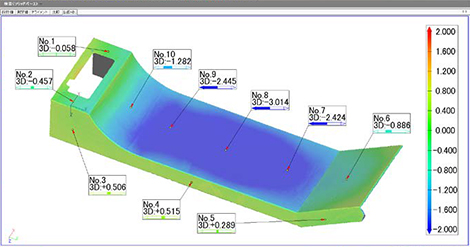
TIGで溶接した製品
(ひずみ量 最大3.01mm)

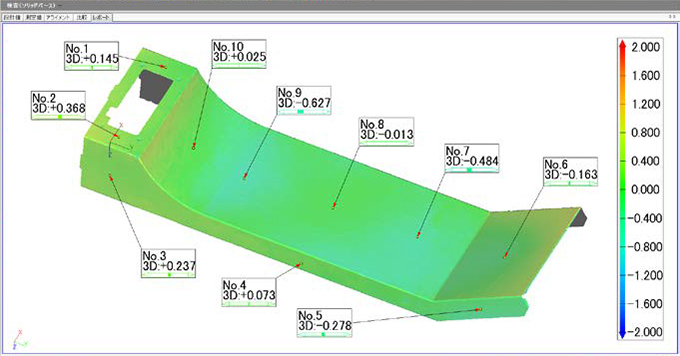
ファイバーレーザで溶接した製品
(ひずみ量 最大0.638mm)
従来の熱でひずんでしまったものを直すのではなく、ひずまない溶接にすることで、ひずみ取りの後工程の工数を大幅に削減し、さらにひずみが取れず作り直すようなムダも激減します。これにより、生産性を大きく向上させることができます。
ここからは、 25年の長きにわたりレーザ溶接システムを運用し続け、さらにFLW-3000ENSISに更新することで大きな成果を上げた企業をご紹介します。
お客さま情報
株式会社 高村興業所様(広島県廿日市市)
■主要事業
精密板金加工部品の設計・製作、機械加工部品、組み付け・組み立て
■主要設備
- ファイバーレーザマシン:
EML-AJ - ベンディングマシン:
ASTROⅡ100NT、HDS-8025他 - レーザ溶接機:
FLW-3000ENSIS、YLR-1500
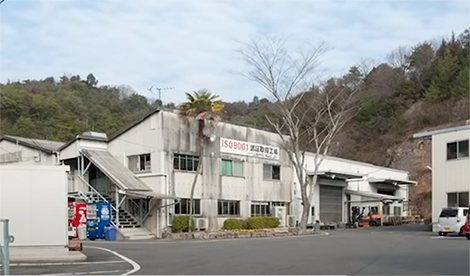
いち早くレーザ溶接を導入
株式会社高村興業所(広島県廿日市市、高村隆晴社長)は、1997年に当時まだ一般に普及していなかったレーザ溶接システム(ロボットタイプ)をいち早く導入され、溶接工程の脱熟練に着手されました。
2004年に、受注量の拡大に伴いYAGレーザ溶接システムを増設して、YAGレーザ溶接を2台体制とすることで生産性が向上し、あらたな得意先の開拓など大きな成果を上げられました。
そして、20年間使用してきたYAGレーザ溶接システム1号機の老朽化に伴い、2018年にファイバーレーザ溶接システムFLW-3000ENSISへ更新しました。
高村隆晴社長にFLW-3000ENSISの導入の感想についてインタビューしました。

高村隆晴社長
FLW-3000ENSISは溶接の複合機
Q1.
FLW-3000ENSISの導入経緯について教えてください。
A1.
溶接職人の育成期間はとても長く、特に半導体製造装置部品などの特殊な溶接をやるためには、さらに育成に時間がかかっていました。
また、半導体製造装置部品の仕事を取り込むため、1997年にYAG溶接ロボットYLR-1500を導入しましたが、導入から20年がたち、機械の老朽化によりメンテナンス費用の増加やランニングコストなどを考慮し、効率の良いファイバーレーザ溶接機の導入に踏み切りました。
Q2.
FLW-3000ENSISで良かった点は?
A2.
これまで使っていたYLR-1500ではできなかったフィラー溶接がFLWではできるようになりました。
しかも、他社のシステムでは共付けとフィラー溶接はプログラムを分け、ノズルなどの段取り換えをする必要がありますが、FLWでは段取り換えなしで、共付け、フィラー溶接、ウイービングスポット※などの様々な溶接ができるため、リードタイムを大幅に短縮することができました。
さながら、FLW-3000ENSISは溶接の複合機のようですね。
※ ウイービングスポット:レーザビームを光学系を用いて回すことで、円形状に溶接できる機能。
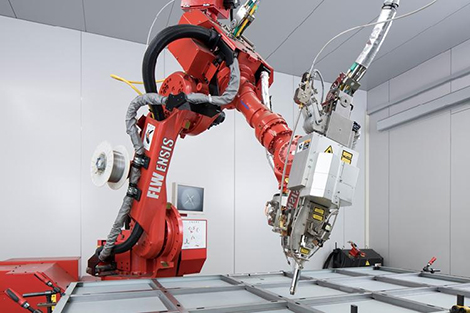
FLW-3000ENSIS
Q3. 具体的な導入効果は?
A3.
美観を要求されるホームドアの加工が、FLW-ENSISを導入することでリードタイムを90%も削減することができました。
これまでは、製品サイズが2000×1000(mm)と大きいため、4人で段取りを行う必要がありました。さらにその後にスポット溶接、TIG溶接で共付け、そして肉盛り溶接を行っていたため、段取りから溶接、仕上げ作業まで98分もかかっていました。
FLW-ENSISの導入後は、スポット溶接と共付け、肉盛り溶接を1台で溶接することができます。これらの工程を1工程に集約できることで、担当は1人で作業を行うことが可能になり、さらに驚くことにリードタイムを10分にまで短縮できました。
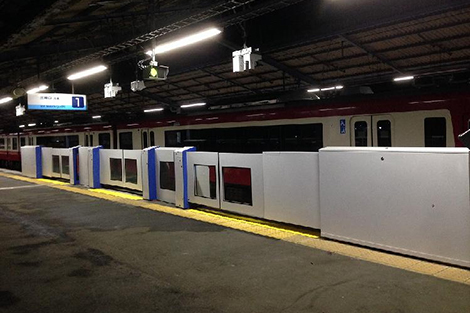
FLW-3000ENSISにて溶接した
ホームドア
Q4. 段取りや仕上げはいかがですか?
A4.
アーク溶接の場合、熱影響を受けてワークがひずむので、しっかり拘束する治具が必要となりますが、ファイバーレーザ溶接では従来のYAGレーザと異なり、焼けひずみの少ない溶接が可能になるため、簡易的な治具を用いて製品を固定するだけで問題なく溶接ができます。今回は溶接後の仕上げ工程はほとんどなしで出荷しています。
Q5. 今後の展望をお聞かせください。
A5.
従来できなかった高難易度な溶接ができるようになったため、今後どのような溶接ができるのかまだまだ試行錯誤中です。
「もう一台購入できないか」と声があがるほど従業員からの評価も高く、インパクトのあるマシンです。
高い評価のウイービングスポット
高村社長からご評価いただいたウイービングスポット溶接は、多くのお客さまから高いご評価いただいております。
あるお客さまでは、保護ビニールをはがし、テーブルスポット溶接で溶接し、焼け取り、最後にキズの処理をしていた製品をウイービングスポット溶接に置き換えることで工数の削減ができました。
FLW-ENSISはアースを用いず溶接するため、保護ビニールをはがす必要はありません。また、意匠面に焼けも出ない溶接条件に設定することで、焼け取りの必要がなく、そのまま出荷できるまでになりました。これにより、段取り工数と担当者の工数の削減につながりました。
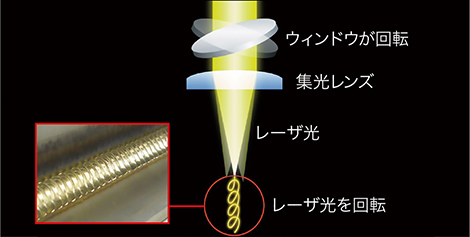
ウイービング機構イメージ
このように、非常にパフォーマンスの高いファイバーレーザ溶接システムです。詳細は以下をご覧ください(動画あり)。