即戦力で活躍する
新しいハンディレーザ溶接機
~ ボトルネック解消で
売り上げが約20%UP ~
注目度が増している「レーザ溶接」
近年、各種自動化設備とならんで注目度が増しているのが「レーザ溶接」です。
マシニスト出版が毎年実施しているアンケート調査の「今後3年以内で設備投資を検討している工程」という設問では、2021年と2022年の2年連続で「レーザ溶接」が最多となりました。
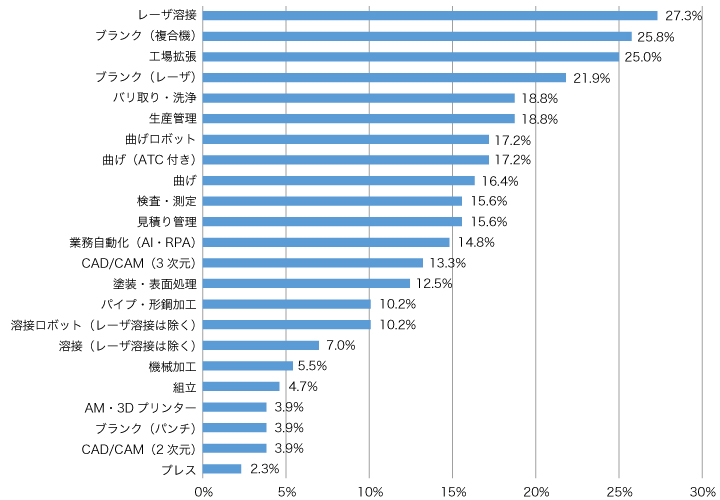
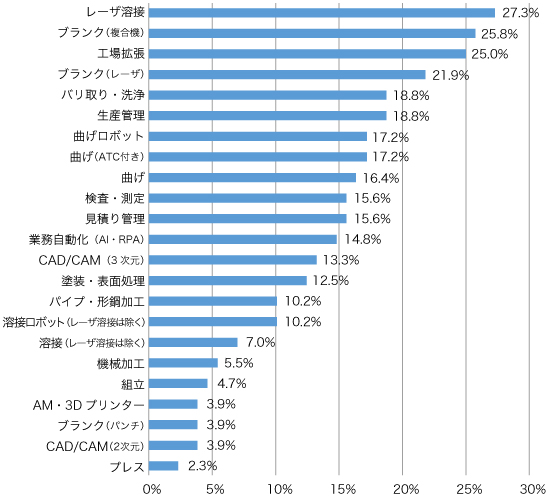
出典:マシニスト出版「Sheetmetalましん&そふと」2022年1月号
レーザ溶接普及の背景①:
熱影響が小さく高品位な溶接ができる
レーザ溶接の普及が加速している要因としては、大きく①熱影響が小さく高品位な溶接ができる、②溶接技能者の不足 — の2つが挙げられます。
レーザ溶接の最大の特長は、母材への熱影響が少なく、従来のアーク溶接と比べひずみ・そりを大幅に低減できることです。溶接ビードが細く、仕上がりが高品位で、とりわけ美観を求められる筐体やカバーに適しています。熱伝導率が高いアルミの溶接や融点の異なる異種材溶接にも比較的容易に対応できます。
板金業界ではYAGレーザ溶接が先行して普及し、その後、ファイバーレーザ溶接へとシフトしてきました。これまで普及が滞っていた理由としては、イニシャルコストが高いこと、溶接ビードが細いためワーク同士の密着精度(すき間の少なさ)が求められること、多品種少量生産に適したハンディタイプだと出力が低く薄板精密の領域に限定されること、出力が大きく加工領域が広いロボットタイプだと治具・ティーチング・段取りなどの要素が加わり多品種少量生産に適用しづらいこと、安全対策のためパーテーションで囲う必要があり、ワークのハンドリングが制約されること — などが挙げられます。
しかし近年は、ハンディタイプであれば高出力化とギャップ対策、ロボットタイプであればギャップ対策やCAM・補正システムなどへの発展によって、上記の「課題」は解消しつつあります。
レーザ溶接普及の背景②:
溶接作業者の不足
現在、高度なスキルと経験が求められる溶接作業者の人材不足は、ますます深刻化しています。
中小製造業はただでさえ人材採用難で、即戦力の経験者を中途採用で獲得することはますます難しくなっています。
ようやく確保できた貴重な人材を溶接作業者として育てようとしても、溶接作業者の場合は育成に多くの時間がかかります。製品の種類や加工内容によって変わってきますが、板金業界の一般的なTIG溶接作業者の場合、指示どおりの溶接を行うための最低限の技能を習得するのに1年程度、図面から必要な作業を判断でき「一人前」と認められるまでに最低でも3年はかかるといわれています。
溶接未経験者の場合、当初は戦力として数えられず、ベテランの先輩社員につきっきりで教わることになります。下積みの期間が長いため、モチベーションを持続させるのが難しく、途中でギブアップするケースも珍しくありません。
溶接は「ひずみとの戦い」
溶接は「ひずみとの戦い」とも言われます。
製品によっては、溶接作業よりも仕上げ作業(焼け取り・ひずみ取り・ビード仕上げ)の時間の方がはるかに長いこともあります。特にひずみ取りは本番の溶接作業と同等かそれ以上のスキルが求められるため、基本的にはベテランの溶接作業者(または組立作業者)が担当しなければなりません。それが溶接工程全体の工数を圧迫し、ボトルネックにつながります。
熱影響を低減するレーザ溶接は、こうした入熱による変形を劇的に抑制することができます。品質向上だけでなく、溶接工程ひいては工場全体の生産性向上と、溶接作業そのものの難易度を大幅に下げることにもつながります。
ボトルネック解消と
溶接作業者の充員が課題
半導体製造装置や工作機械向けの板金部品加工を主に手がける(株)トーコー(山梨県富士吉田市、渡辺裕治社長)は、新しいハンディファイバーレーザ溶接機「FLW-1500MT」を活用することで大きな成果につなげています。
「溶接工程のボトルネック解消」と「溶接作業者の充員」は、同社にとって長年の課題でした。
熱影響を受けやすいアルミやステンレスの薄板カバーや、サイズが大きいパネルを多く手がけているため、仕上げ作業が溶接工程・組立工程の大きな負担となっていました。また、溶接工程のメンバーは溶接経験25年以上のベテランがほとんどで、現時点でのスキルは申し分ないものの、将来を見据えた人材育成も必要でした。
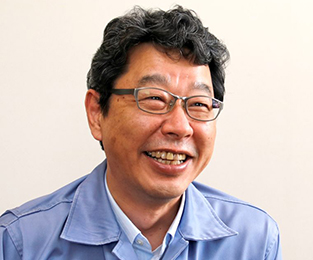
渡辺裕治社長
加工領域を大幅に拡大した
「FLW-1500MT」
これらの課題を解決するために導入した「FLW-1500MT」は、多品種少量生産に対応しやすいハンディタイプにもかかわらず最大定格出力1500Wに高出力化し、従来機種と比べ加工領域(対応板厚や溶け込み能力)が大幅に拡大しました。
また、光の周期・振幅を自由に可変する「ウォブリング機能」を搭載し、すき間(溶接ギャップ)への対応力向上、フィラー溶接の安定化などを実現しています。ウォブリング機能とフィラー溶接を採用することで、多少のすき間であれば余裕をもってカバーできます。完全空冷方式のチラーレスで、チラーのメンテナンスが要らないのも特長です。
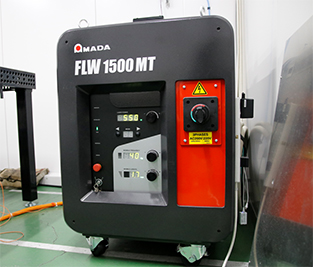
「FLW-1500MT」
溶接未経験者が即戦力に
新たに導入した「 FLW-1500MT」の担当者は、30歳の加賀美浩大さん。入社12年目ですが、ずっとブランク工程を担当していたため、溶接経験はありません。TIG溶接であれば最初は先輩社員がつきっきりになるところですが、同社では今のところTIGと「FLW-1500MT」を併用するケースが多いこともあって、加賀美さんはすでに一人で作業しています。
「これはTIGでもできる」「ここはファイバーレーザ溶接の方が良い」といった判断はベテランが行い、加賀美さんに仕事を受け渡すときに指示や助言をしています。
仮付けはベテランがTIGで行い、本溶接は加賀美さんが「FLW-1500MT」で行い、その後のチェックと仕上げは再びベテランが行うケースもよくあります。
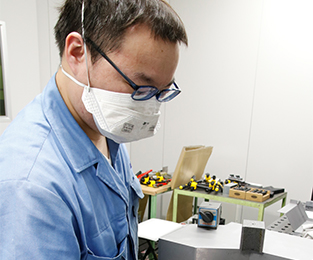
加賀美浩大さん
前田忠則リーダーは「こうして溶接工程の中で分業をすることで、ベテランから経験の浅い社員へ溶接のスキルや考え方を伝えることができます。『火を出す時間』も以前より長く取れるようになって、全体の生産性もアップするという好循環になっています」と語っています。
「FLW-1500MT」が搭載している「溶接作業者を支援する各種機能」について、前田リーダーは次のように評価しています。
「溶接条件の設定はタブレット端末から行えます。タブレット端末のアプリのメニューから、材質・板厚・溶接方法(隅肉、フィラーなど)などを選択し、必要に応じて出力を調整するだけで、トライなしで本番の溶接ができます」。
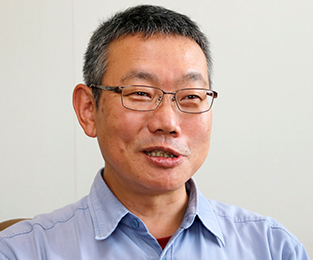
前田忠則リーダー
「カーボンノズルは、母材とトーチ先端のギャップをコントロールする必要がなくなるので、定規で線を引く感覚で溶接できます。I形の溶接の場合、ガイドを置いて、線を引くように引っ張るだけ。角溶接も、専用のカーボンノズルを用意すれば、ワークに沿わせながら線を引く感覚で溶接できます」。
「ウォブリング機能(最大5mm幅)は最も重視した機能のひとつです。従来のレーザ溶接の弱点を補う機能で、この機能がなかったら導入は見送っていたかもしれません。ウォブリング機能を使うことで、多少のすき間であればカバーしてくれます。ウォブリング機能とフィラー溶接があれば、たいていのすき間は埋められるので、実務上困ることはないと思います」。
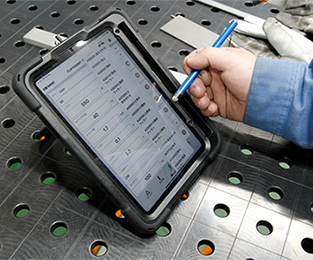
タブレット端末
ボトルネック解消で
売上高約20%アップ
熱による変形(ひずみ・そり)を大幅に低減できるファイバーレーザ溶接で加工することにより、生産性が大きく改善した製品もあります。
たとえば、半導体製造装置向けの「ステップ」は、曲げによる一体構造から溶接構造に工法転換。全周溶接でも溶接ひずみがほとんど出なかったため、曲げ加工後に実施していた下穴加工とタップ加工をブランク工程で行えるようになり、全体の工数を約25%削減できました。
工作機械向けの「カバー」は、気密性能が求められ、TIG溶接後のコーキング作業が必要でした。これをTIG溶接から「FLW-1500MT」による全周溶接に変更することで、気密性を確保しつつコーキング作業を省略。全体の工数を20%程度削減できました。
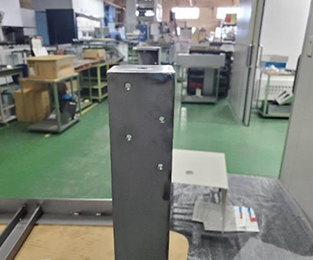
半導体製造装置向けフレーム
加工材料の20%を占めるアルミのカバー類について、前田リーダーは「アルミは熱影響を受けやすいので、優先的に「 FLW-1500MT」で溶接しています。TIG溶接だと常に不安がつきまとっていましたが、 「 FLW-1500MT」だとひずみ取りの作業がほとんど要りません。角度もしっかり出ています。ビードが細くても裏波がしっかり出ていて、強度も十分です」と語っています。
渡辺社長は「売上高ベースで20%ちかくアップしました。これまでだったらやりきれなかった仕事まで、こなせるようになったイメージです。ボトルネックだった溶接工程を増強したかたちですが、TIG溶接だったら溶接経験のない社員をいきなり投入してもすぐには効果が出ません。「FLW-1500MT」を導入したことによって溶接未経験者が即戦力となり、ネック工程がスムーズに流れるようになってくれたのはきわめて大きいと感じています」と語っています。
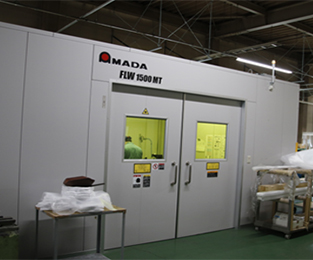
「FLW-1500MT」の溶接ブース
「先行投資」から本格的な普及段階へ
これまで板金業界では、加工範囲(対応板厚)の都合により、ハンディタイプよりもロボットタイプのレーザ溶接機の方が強い存在感を示してきました。しかしここへきてハンディタイプのファイバーレーザ溶接機も高出力化に対応し、溶接作業者を支援する様々な機能が充実してきたことで、多品種少量生産の板金加工でも十分な実用レベルに到達したといえます。
以前は、アーク溶接からレーザ溶接への工法転換を得意先メーカーに認めてもらえず、せっかくレーザ溶接を導入しても適用できないケースがよくありました。しかし、レーザ溶接が徐々に浸透してきたことで、今では図面上で「ファイバーレーザ溶接」を指定されるケースも増えています。
今やファイバーレーザ溶接機は「先行投資」の段階から一歩進み、時代と顧客の要請に応えるための有力な選択肢として、いよいよ本格的な普及段階に入ったといえるでしょう。
記事:マシニスト出版