「架台・フレーム」の
生産プロセス改革
~ 平板・パイプ兼用レーザマシンが
生産合理化に貢献 ~
「架台・フレーム」の加工は
多くの改善余地を残している
「架台・フレーム」の領域は、機械化・デジタル化が遅れ気味で、多くの改善余地を残しています。
熟練技能者の経験と技能に頼る部分が大きいためコスト(工数)がかかり、生産量が増える局面ではボトルネックになりがちです。また、人手不足・職人不足が深刻化していることから、難易度が高い架台やフレームの加工は合理化と簡易化がますます強く求められています。
板金加工企業にとっては、ワンストップ対応を求められる傾向が強まり、対応領域が広がっているという側面もあります。カバーや子部品といった板金加工部品だけでなく、架台やフレームを含む筐体一式、場合によっては電装組付を含むOEM供給までを要望されるケースが増えており、架台やフレーム加工への対応を検討する必要が生じています。
板金部品とセットで用いられる
「架台・フレーム」
一般的に、高い剛性・強度が必要となる産業用設備は、パイプ・形鋼で組み上げられた架台やフレームと、板金加工で製作したカバーや子部品で構成されます。パイプ・形鋼の規格品では対応できないフレーム形状の場合は中厚板を曲げて製作した板金フレーム、得意先の設計方針によってはコストダウンのために押出成形材などを用いるケースも見られます。
代表的なフレーム構造の製品は、キュービクルや配電盤といった受配電設備や通信機器ラックなどで、チャンネル(溝形鋼)やアングル(山形鋼)といった形鋼フレームを用いて製作します。建設機械や農業機械などのフレーム、工作機械・半導体製造装置・食品機械といった産業用設備の架台やフレーム、搬送装置やステップといった工場設備の架台やフレームでも、パイプ・形鋼が多用されます。
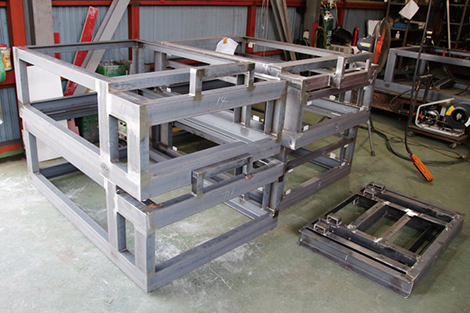
溶接組立が完了したフレーム架台
写真: (有)シルバーポート
「架台・フレーム」の加工プロセス
架台やフレームの加工は通常、パイプ・形鋼に対して「①切断・切り欠き」「②穴あけ・タップ加工」「③溶接組立」の順に作業を行っていきます。
パイプ・形鋼に対応するレーザ加工機(後述)がない場合、「①切断・切り欠き」はメタルソーやバンドソー、アイアンワーカーなどで加工します。ただし、メタルソーやアイアンワーカーの場合、加工時に引っ張られて曲がったり、ひずんだりと変形しがちなため、後工程で矯正する作業が発生します。
「②穴あけ・タップ加工」は、寸法を計測し、ケガキを入れたりガバリを当てたりして位置決めをしてから、ドリルやボール盤で加工します。ただし、食品機械や半導体製造装置などで用いられるステンレス製の架台やフレームの場合は、R形状の切り欠きや長穴などはフライスなどの機械加工で対応する必要があり、コストが高くなりがちです。
「③溶接組立」は、ケガキ線に合わせてクランプなどで固定し、仮溶接を行って、対角寸法などをチェックしてから本溶接を行います。ただし、ケガキによる位置決めはずれやすく、直角に組み付ける際の角度調整も容易ではありません。
母材の精度のバラツキ、「①切断・切り欠き」「②穴あけ・タップ加工」で生じた変形や誤差、溶接の熱影響などで生じたひずみなどは、すべて最後の溶接作業者が調整して仕上げなくてはなりません。これだけの作業を行うためには熟練の技能はもちろんのこと、重量物であるパイプ・形鋼を取り回す体力も必要になり、人材の確保と育成を難しくしています。
兼用レーザマシン加工機が
生産合理化・早期戦力化に貢献
平板・パイプ・形鋼に対応したレーザ加工機は、溶接製缶も手がける板金加工企業にとって有力な選択肢となります。
レーザビームによる非接触加工で自由形状に対応できるため、切断・切り欠き・穴あけを1台で完結できます。また、加工による変形が少なく正確に切断でき、長穴・R形状・ケガキ線も手軽に加工できます。
また、位置決め用の突起と差し込み穴を加工してはめ合い構造にすることで、溶接組立の際の寸法測定と位置合わせが不要になります。“プラモデル感覚”で組み上げられるようになるため、技能を持たない作業者の早期戦力化にも貢献します。
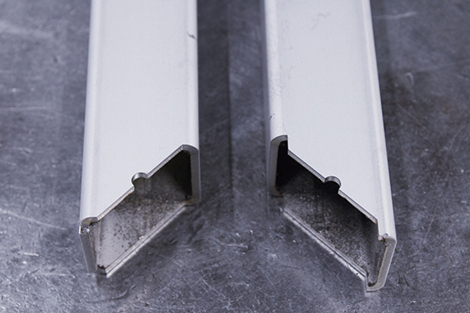
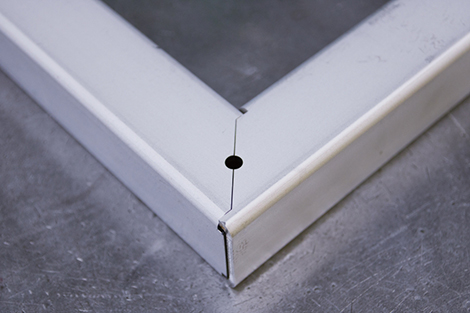
ファイバーレーザ加工機「ENSIS-RI」で
加工したステンレスの角パイプ
はめ合い構造とし、接合部に半円を加工することで
合わせたときに丸穴になる
写真:(有)藤田製作所
パイプ・形鋼に特化した高機能の「専用レーザ加工機」も存在しますが、設置スペースや稼働率の関係で、小規模な板金加工企業ほど採算ラインに載せるのが難しくなります。そのため、中小の板金加工企業の間では、平板とパイプ・形鋼の両方を切り替えながら使用できるオールラウンドな「兼用レーザ加工機」の普及が進んでいます。
ここからは、アマダの平板・パイプ兼用ファイバーレーザ加工機 「ENSIS-3015RI」(3kW)を活用することで、架台やフレームの生産プロセスを劇的に改善した事例を3件、ご紹介します。
「溶接組立は信じられないくらい楽になった」
(株)中野屋ステンレス(長野県伊那市、小坂博志社長)は2019年、平板専用の「FO-3015NT」(CO2レーザ・4kW)との入れ替えで「ENSIS-3015RI」(パレットチェンジャー仕様)を導入し、平板の加工領域を拡大しつつ、パイプや形鋼の加工能力を増強することに成功しました。
同社の主要製品は、工作機械に使われるクーラントろ過装置で、中部圏に本社を置く装置メーカー2社向けにOEMで供給しています。続いて多いのがLEDを使った標示装置で、板金筐体の加工・塗装まで行ってから納品します。このほかにも、コンビニエンスストアのサインスタンド、建築金物、集塵装置、飲料用充填機などのユニット・部品、環境機器などを手がけています。
ワンストップ対応を強みとしていることから、得意先のニーズが増えているパイプ・形鋼の加工を強化するため「ENSIS-RI」を採用しました。とはいえ、平板の加工が約80%、パイプ・形鋼の加工が約20%で、メインはあくまで平板。そのため、「パイプ・形鋼の専用機ではなく、どちらにも使える『ENSIS-RI』の方が投資メリットが大きい」(小坂賢一専務)と考えました。
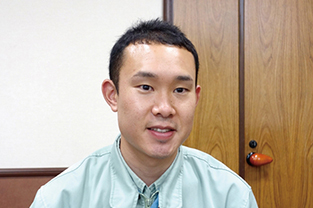
小坂賢一専務
FOから「ENSIS-RI」に変わり、 CO2レーザがファイバーレーザになったことで、機械単体の電気使用量は約60%減りました。工場全体の電気使用量も35.9%減となり、金額にすると年間470万円ほど削減できました。
「溶接組立は信じられないくらい楽になりました。労力で考えると、2~3倍は違ってくると思います」と小坂専務は語っています。
「以前は、寸法どおりにメタルソーで切断し、ケガキを入れて穴を加工し、溶接して、対角寸法を測って、修正してと、大変な手間がかかっていました。メタルソーで切断すると材料の反りなどが発生するため、製品としてまとめるためには熟練工の勘と経験が欠かせませんでした」。
「『ENSIS-RI』を導入してパイプや形鋼の加工精度が高まると、溶接組立の精度が改善し、工数も大幅に減りました。溶接担当者は『組んだときの対角寸法の精度がまったく違う。なおす必要がない』と驚いていました。今では、単純なフレームの組み立てなら、熟練工に頼ることなく経験が浅い社員でも調整なしで対応できます」(小坂専務)。
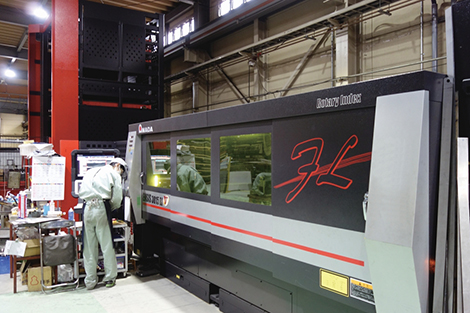
2019年に導入した「ENSIS-3015RI」
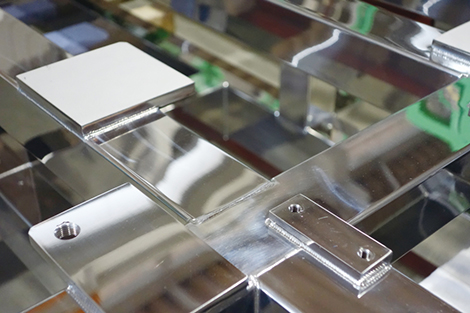
半導体製造装置の架台(SUS304)
ホゾ・ミゾを加工して溶接作業を簡便化
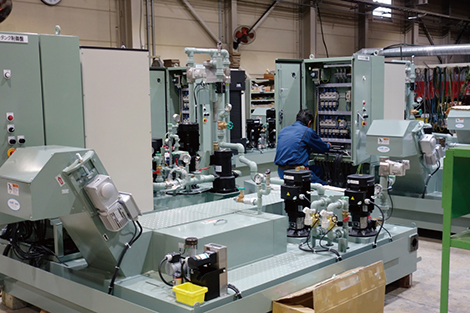
工作機械用のクーラント装置や
チップコンベアの組立工程
「中小規模の製缶板金企業にとって
強力な武器になる」
環境試験機・乾燥炉などの「装置事業」と、受託加工の「製缶板金事業」を展開している(有)シルバーポート(埼玉県坂戸市、桜井成丸社長)は、2016年に平板・パイプ兼用レーザ加工機「FO-MⅡ RI 3015」(CO2レーザ・4kW)を、2019年に「ENSIS-3015RI」を導入しました。
「FO-MⅡ RI」は、「装置」「製缶板金」のいずれもパイプや形鋼の使用割合が高かったため導入し、すぐにフル稼働するようになりました。特にステンレスの形鋼を手軽に加工できるのは大きく、それまでは協力工場に機械加工を依頼していた部分も、すべて社内で対応できるようになりました。
桜井成丸社長は「溶接組立の生産性は劇的に改善しました。それまではバンドソーやアイアンワーカーでパイプや形鋼を切断し、溶接組立の際は寸法を測りながら合わせていました。 『FO-MⅡ RI』を導入してからは、位置決め用のレーザケガキや切り欠きを加工することで、溶接作業者は迷うことなく組立ができるようになりました。寸法を測る必要がないため作業スピードが上がり、組立精度も向上しました。経験が浅く、図面を読めない社員でも、簡単な立体図をつけてあげれば溶接組立ができるようになりました」と振り返ります。
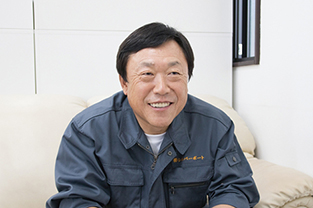
桜井成丸社長
2019年秋、令和元年東日本台風(台風19号)による洪水被害で、導入後3年しか経っていない「FO-MⅡ RI」は水没し、そのまま廃棄となりました。しかし、桜井社長はその約2カ月後、早くも「ENSIS-3015RI」の導入を決断しました。
「『FO-MⅡ RI』を失ってみて、その存在の大きさをあらためて認識しました。被災してから約2カ月の間は、バンドソーやアイアンワーカーで加工していましたが、生産性が極めて低く、ほとんど仕事になりませんでした」(桜井社長)。
「FO-MⅡ RI」から「ENSIS-RI」になって大きく変わったのは「電気料金」でした。省エネ性能が高いファイバーレーザになったことで、工場全体の電気料金は30%以上も減少しました。
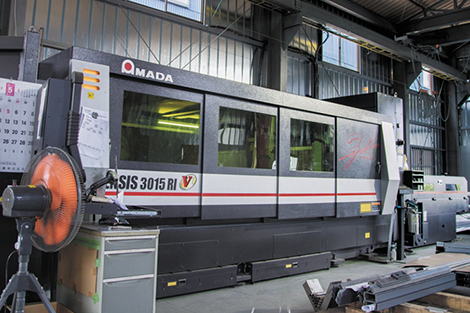
2019年12月に導入した
「ENSIS-3015RI」
また、「FO-MⅡ RI」にはなかったサポートチャックの同期運転とタッチプローブ機構により、さらに高い精度で加工できるようになりました。C型チャンネルを加工できるようになったのも大きなメリットでした。C型チャンネルは板厚が薄いためねじれやすく、メインチャックしか回転しない従来の「FO-MⅡ RI」では加工ができませんでした。
「『ENSIS-RI』は、当社のような中小規模の製缶板金企業にとって、まちがいなく強力な武器になるマシンです。大きな会社だと、平板を加工している間、パイプや形鋼を加工できないことを嫌がる場合もあるかもしれませんが、当社くらいの規模だと“兼用”がちょうど良い。平板とパイプ・形鋼の切り替えの時間や手間も気になりません」(桜井社長)。
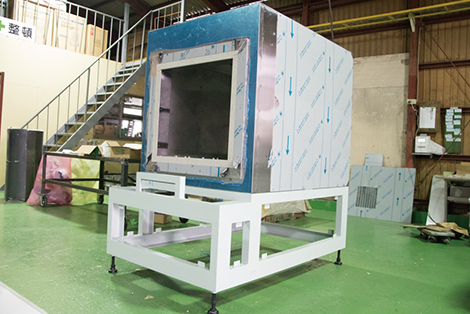
「装置事業」の製品
環境試験機の筐体
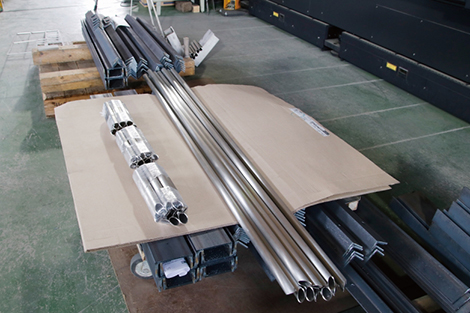
ENSIS-RIで加工した
パイプ・形鋼
「全体の工数は半分に ―
コロナ禍でも入れて正解」
食品機械で使用するステンレス製缶板金を主に手がけている(有)藤田製作所(埼玉県入間市、藤田幸男社長)は、2020年6月に「ENSIS-3015RI」を導入し、板厚6.0mm超の中厚板とパイプや形鋼の加工能力を強化しました。コロナ禍で一時的に業績が大きく落ち込んでいる時期でしたが、藤田幸男社長は「導入して大正解。現場の作業工数は約半分になりました」と評価しています。
同社が手がける食品機械は、1台あたり長さ2~3m。これを現地で連結すると、長いもので十数mの食品製造ラインになります。一品一様の典型的な多品種少量生産で、パイプや形鋼のフレームと、それに付随する板金部品を加工し、溶接組立を行ってから、機械加工とアセンブリーを行っている組立企業に納めています。
平板、パイプ、形鋼とも約90%がステンレス(SUS304・SUS430)。パイプ・形鋼は、アングルと角パイプの割合が高く、アングルだと40×40mm(板厚5mm)、50×50mm(板厚6mm)、角パイプだと板厚2mmの50×50mm、100×100mm、50×100mmを多く使用します。
「ENSIS-RI」の導入効果として特に大きかったのは「内製化」です。
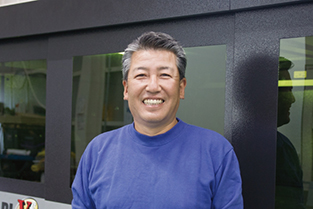
藤田幸男社長
ステンレスのパイプ・形鋼に長穴を加工したり、チャンネルにR形状の切り欠きを入れたりする場合、以前は協力会社に機械加工を依頼するしかありませんでしたが、「ENSIS-RI」導入後は社内で完結できるようになりました。協力会社に依頼するのは、H7公差の穴加工のような、機械加工でなければ対応できない加工だけになりました。
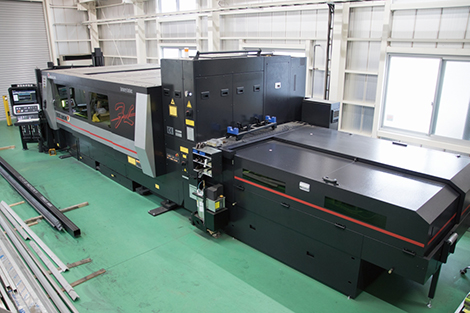
2020年6月に導入した「ENSIS-3015RI」
内製化できた分、製造リードタイムは短くなり、納期対応力も増しました。また、外注費が減ったことで原価を低減でき、コスト競争力も高まりました。
生産効率も劇的に改善しました。以前は、アイアンワーカーやバンドソー、メタルソーでパイプ・形鋼を切断し、レーザマシン 「LC-αⅣ NT」やボール盤で穴あけを行っていました。切断と穴あけが別工程で、作業者によって作業時間のバラツキが発生していました。それが今では「ENSIS-RI」だけで完結できるようになり、加工時間が予測できるようになりました。
また、架台やフレーム筐体の場合、位置決め用の切り欠きを入れてはめ合い構造にすることで、寸法を測ることなく正確に組み上げることができるようになりました。
「切断・穴あけの作業だけで1日半かかっていた仕事が、今では1日かかりません。労力の面も大きく、以前は定尺のパイプや形鋼を手で持ち上げてアイアンワーカーやメタルソーにセットしていましたが、今は天井クレーンで吊り上げ、『ENSIS-RI』に搬入するだけ。その後の溶接組立の効率アップも考えると、全体の工数は半分くらいになったと思います」(藤田社長)。
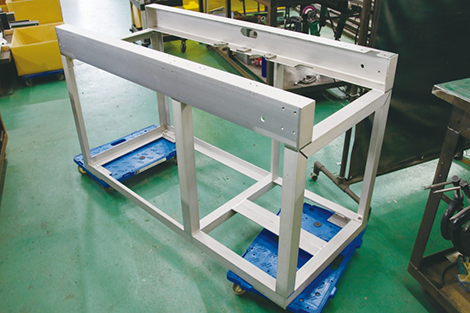
オールステンレスの食品機械フレーム
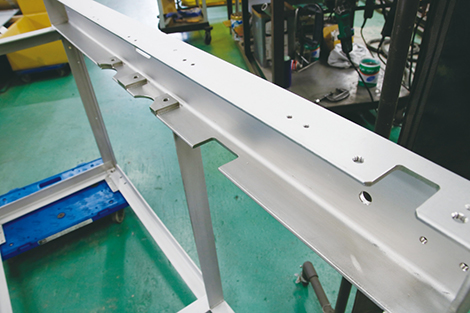
チャンネルの切り欠きは、ほかの装置とドッキングする際に使用する
今も先行者利益を期待できる領域
「ENSIS-RI」を導入した企業からたびたび聞かれるのが、「導入するときは採算が取れるか不安だった」という言葉と、「導入してみたら効果の大きさに驚いた」という言葉です。ここには、通常のファイバーレーザマシン(切断)やパンチ・レーザ複合マシンと比べると導入事例が少ないことと、専用機を導入するほどのボリュームがないところへ「兼用レーザ加工機」を導入したときの効果を予測するのが難しいといった事情がありそうです。
中には普及率の低さを逆手に取って、「溶接専業の協力工場と折り合いがつくようなら、『ENSIS-RI』で加工したパイプ・形鋼を支給して強みを生かしたい」であるとか、「『ENSIS-RI』でプレ加工を行い、鋼材商社などを通じて設備を持たない溶接工場などに販売したい」のように、他社との差別化や新しいビジネスにつなげていこうとする動きも見られます。
架台やフレームの加工は機械化が遅れているからこそ、今でも先行者利益を期待できる領域といえます。それも踏まえて、レーザ加工の採用を含めた合理化・簡易化の検討が必要になっていきそうです。
記事:マシニスト出版
「架台・フレーム」加工を合理化・簡易化する
「ENSIS-3015RI」の詳細はこちら