工場全体の改善改革に
貢献するIoT
~ 板金業界に浸透する
アマダのIoT ~
IoTソリューションの普及が進む
2010年代は世界の産業界全体で「デジタル化」が叫ばれた10年間でした。
2011年にドイツ政府が国家戦略として「インダストリー4.0」を提唱し、そのコンセプトは2013年開催の産業見本市「ハノーバーメッセ」を通じて日本にも大きなインパクトを与えました。その後、「IoT」※1、「AI」 、「ビッグデータ」などが脚光を浴びるようになり、製造業など“現場”のデジタル変革を促す「スマートファクトリー」※2や「デジタルトランスフォーメーション」※3(DX)の潮流が生まれました。
製造業において、「様々なモノがインターネットにつながる」ことを目指す「IoT」は、スマートファクトリーや工場DXの基盤となる仕組みとして、2014年頃からメディアや産業界で頻繁に取り上げられるようになりました。
その後は、あらゆる産業分野で生産財メーカー各社が独自のIoTソリューションを立ち上げ、普及が進んでいきました。各メーカーでは今のところ、横断的なオープンIoTプラットフォームを活用したり、中小製造業の間では生産財メーカーが提供するIoTソリューションを利用するケースが一般的です。
- ※1:IoT=様々なモノがインターネットに接続されデータがやり取りされる仕組み(Internet of Things)
- ※2:スマートファクトリー=デジタル技術の活用により業務プロセス改善や品質向上、生産性の最適化を実現している工場
- ※3:デジタルトランスフォーメーション=デジタル技術を活用してビジネスモデルを変革し、競争上の優位性を確立すること
アマダのIoT「V-factory」が
急速に浸透
板金業界では、2018年から本格展開を開始した板金加工に特化したアマダのIoT「V-factory」が急速に浸透しています。
「V-factory」は、加工マシンの稼働を支援する「IoTサポート」と、生産プロセスの“見える化”を実現する「My V-factory」という2つの機能で構成されています。
「IoTサポート」では、「IoTサポートセンター」によるリモートでの予防保全提案と早期復旧支援、アラームの繰り返し発生を予防する運用改善提案などを行い、稼働率改善を支援します。
「My V-factory」では、マシンの稼働状態、稼働実績、生産実績を“見える化”し、稼働率の全国平均や自社の全国ランキングを確認できます。
材料やエネルギーの使用量、マシンごとの健康状態や不稼働要因、運用分析も行えます。
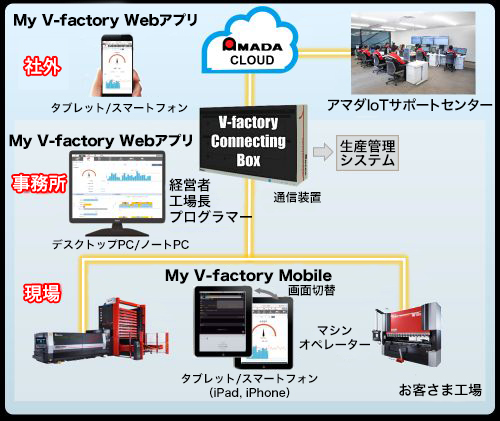

「V-factory」の運用イメージ図
工場全体の改善改革に貢献するIoTの効能が認知されるようになったことで、「V-factory」の利用企業は世界で1500社を超えました。つながるマシンは4000台を超え、さらに広がりを見せています。
ここからは、板金業界のIoT実践事例として、「V-factory」の「IoTサポート」(稼働支援)と「My V-factory」(見える化)を活用している企業をそれぞれ1社ずつ紹介します。
「IoTサポート」の活用で
稼働率を改善
まずは「IoTサポート」(稼働支援)の活用事例として、防音パネル、防音ボックス(エンクロージャー)、受配電盤を主に手がける(株)たつみ電機製作所(静岡県富士市、佐藤和亘会長)をご紹介します。
同社は2021年1月、ファイバーレーザ複合マシン「EML-Z2515AJ」を導入しました。本機は、4000×1500mmまでの材料に対応する特殊仕様で、自動金型交換装置(PDC)、8段のサイクルローダーとテイクアウトローダー(ASR-3015NTK)付きの自動化システムとなっています。
さらに、インターネットにつながる「V-factory」に標準で対応する「Vfマシン」であり、同社では「IoTサポート」のチャットによる問い合わせ機能をフルに活用し、「EML-AJ」を運用する過程で発生した疑問や不具合を素早く解消することに役立てています。
佐野雄彦社長は、「『EML-AJ』は当社の中核設備として導入したため、一日でも早くフル稼働してもらう必要がありました。そのため、稼働を支援する『IoTサポート』は『EML-AJ』の早期立ち上げを実現するサービスとして期待していました」と語っています。
主に展開・プログラムを担当している製造一課の渡辺聡彦係長は、「IoTサポート」を活用することで「EML-AJ」のオペレーションを後方から支援・管理しています。
「IoTサポート」のチャットによる問い合わせ機能の活用実績は、約1年の間に285件もの問い合わせ数にのぼり。これは「V-factory」に接続している全国の企業の中でもトップクラスの問い合わせ件数といえます。
渡辺係長が問い合わせる内容は、大きなトラブルというよりも、金型・オイル・グリス・集塵機なども含めたちょっとした不明点など、些細な問い合わせが大半を占めています。
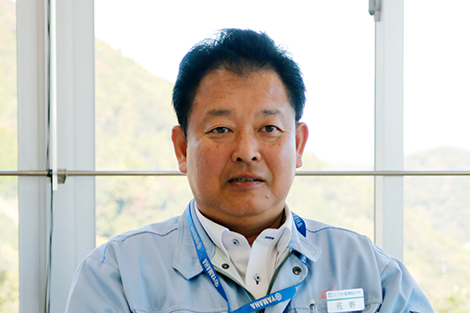
佐野雄彦社長
例えば、PDCに収納していた金型(ダイ)が出てこず、加工がストップしてしまったケースでは、「IoTサポートセンター」に問い合わせた結果、その金型は使用頻度が極端に低く、使用していない数カ月の間にオイルが固まってしまったことが原因だとわかりました。また、クランプする個所に切り欠きがあるワークの処理方法を問い合わせた場合は、Mコードに追記することでクランプ位置を変更する方法を知ることができました。
このような、「IoTサポート」で問い合わせた内容はデジタルデータとして記録されるため、会社の“ナレッジ”として蓄積・管理でき、教育訓練のツールとしても役立てることができるようになりました。
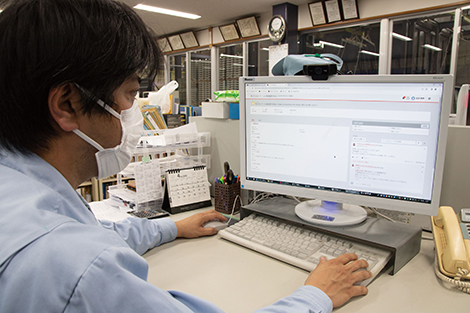
IoTサポートをフル活用する渡辺係長
渡辺係長は「細かな疑問は、実際に運用している中で次々と出てきます。しかし、サービスマンを電話で呼び出すほど深刻な問題ともいえません。これまでだったら、運用サイドが、手作業に切り替えたり別のマシンで加工したりして吸収するか、工数をかけてトライ&エラーで経験則を身につけるといったケースも多かったと思います。チャットによる問い合わせは心理的ハードルが低く、疑問が生まれたら迷わずすぐに問い合わせることができます。だいたい30分以内にレスポンスをもらえるので、よほどはっきりした故障でもない限り、サービスマンに電話をすることはありません」。
「いちいちテキストを入力しなければならないのは、たしかに手間です。しかし、共有・引き継ぎ・検索といった後々の利便性を考えると、できるだけ記録が残るかたちで問い合わせるのがベストです。それに、チャットの画面ではテキストだけでなく写真や動画、図面や見積書といった各種ドキュメントも手軽にやりとりできます。これは、オンラインコミュニケーションの一番の強みだと思います」と語っています。
佐野社長は「問い合わせ先の『IoTサポートセンター』が身近に感じられるようになったことで、当社の問い合わせ件数が増えているのだと思います。
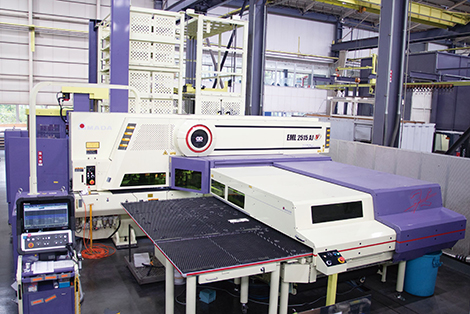
2021年1月に導入した「EML-AJ」
『サービスマンに電話をかけるほどでもないかな』とか『別の用事でサービスマンが来たときについでに聞いてみよう』とか、そういった遠慮をすることなく、すぐに問題を解消できるのはありがたいと感じます」と評価しています。
「My V-factory」の活用で
改善改革を推進
続いて、「My V-factory」(見える化)の活用事例として、工作機械関連やプラント・原動機関連を主に手がける(有)山之内製作所(群馬県太田市、萩本道久社長)を紹介します。
同社は、2018年に萩本道久社長が就任して以来、コロナ禍をはさみながらも立て続けに大胆な設備投資を実施。自動化技術・デジタル技術を採り入れたスマートファクトリーへの変革を目指し、工場改革を推進しています。
2019年に導入した「HG-2204ATC」が、「V-factory」に標準で対応する「Vfマシン」だったことから、既設のネットワーク対応型マシンもすべて「V-factory」に接続しました。「My V-factory」によって稼働状況・生産実績の“見える化”を実現し、萩本社長を含む事務所のメンバーが製造現場の状況を直接把握できるようになりました。
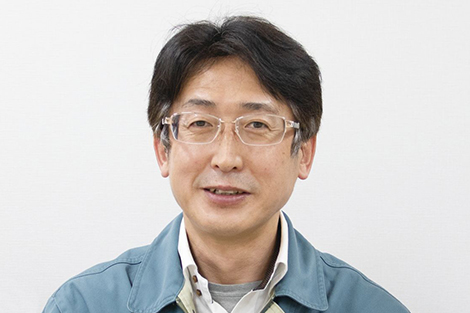
萩本道久社長
プログラム工程を担当する中谷孝行さんは「『My V-factory』でよくチェックしているのは『マシン別稼働実績』の画面です。特に『EML-AJ』は導入して間もないので、どういうプログラムのときに、どういうアラームが発生したのかを確認し、現場スタッフのコメントと合わせて対策を検討しています。『EML-AJ』は稼働監視カメラ『V-monitor』も装備しているため、アラームが発生した時点までさかのぼって映像をチェックすることもあります」。
「生産実績をリアルタイムで確認できるメリットも大きいと感じます。これまでは、溶接・組立工程の作業者や配膳担当者から『この部品が届いていない。確認してほしい』と問い合わせがあると、一つひとつ工程を追いかけていく必要がありました。
ブランク工程のどのシートに板取りされていたか、曲げ工程は終わっているか、不良が出たか出なかったかなど、調査に多くの時間を取られてしまい、本業のプログラム作業にも支障が出ていました。しかし今は『My V-factory』の画面を開けば、ブランク・曲げに関してはどの製品に着手して完了したか、すぐに確認できます。それだけでも工場全体の効率が劇的に改善しました」と語っています。
また、マシンが稼働していない時間や停滞している時間を事務所スタッフが直接把握できるようになったことで、事務所スタッフと現場スタッフが協力して改善方法を考えられるようになりました。
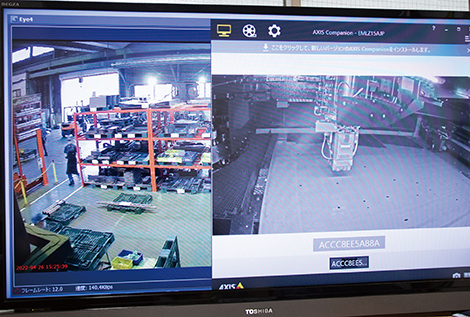
ネットワークカメラによる本社工場の様子(左)
「V-monitor」による「EML-AJ」の機内(右)
例えば、「HG-ATC」は段取り換えが多くなる小ロット~中ロット品を中心に加工しているため、萩本社長は当初、ショット数よりも品目数と段取り時間の相関を意識してチェックしました。その結果、月間の「平均加工時間」や「平均加工品目数」が伸びても、「平均段取り時間」はほとんど増えておらず、狙いどおりの運用ができていることを確認できました。しかしその反面、「平均ショット数」は想定外に伸び悩んでいたため、その事実に基づいて工場内のレイアウト変更と運用改善に踏み切りました。
これまでは、本社工場と第2工場の間で頻繁に横持ちが発生していましたが、第2工場に「EML-AJ」と曲げ工程、溶接工程(手溶接)を集約し、主に板厚6.0mm以下の製品はひとつの工場建屋で完結できる体制にしました。さらに、これまでは曲げ・溶接の作業者がみずから加工する製品を引き取りに行っていましたが、新たに配膳担当者を配置することで、曲げ・溶接の作業者が本来の作業に専念できるようになりました。
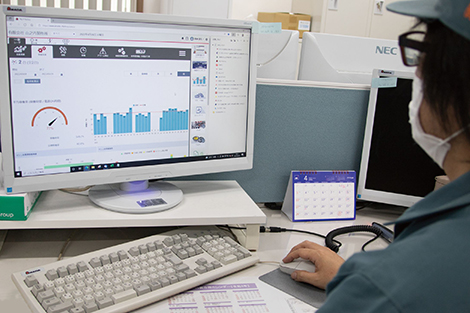
プログラム工程担当の中谷孝行さん
萩本社長は「『My V-factory』のデータに基づいて工場全体の整流化をはかったことで、ボトルネックだった曲げ・溶接工程の生産性は大幅に改善しました。これまで30%程度を占めていた曲げ・溶接の外注比率は、現在は20%以下に削減でき、その分、利益率も改善しました」と評価しています。
「V-factory」の両輪
ここでは「V-factory」を構成する「IoTサポート」(稼働支援)と「My V-factory」(見える化)の効能がわかりやすく伝わるように、どちらか一方を重点的に活用し、成果を出している事例を紹介しました。
事例からもわかるとおり、「IoTサポート」は現場オペレーションの過程で稼働率を押し下げる“ネガティブな要素”を取り除くための機能、「My V-factory」は生産プロセスを“見える化”して、生産性改善につながる“ポジティブな要素”を積み上げるための機能として、「V-factory」の両輪をなしていると言えるでしょう。
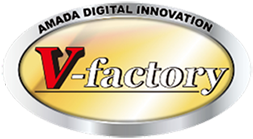
IoTという言葉が使われ始めた当初は一部で懐疑的な見方もありましたが、「V-factory」は今や工場運営に欠かせないサービスとして定着しつつあります。加工に携わるオペレーターにとっても、稼働率や全国ランキングといった客観的なデータがモチベーションにつながるケースが多く見られます。先端的な事例としては、複数拠点のリアルタイム管理や、企業間連携のプラットフォームとしての活用も模索されており、IoTの活用ノウハウはますます重要になっていきそうです。
記事:マシニスト出版