鉄道車輌業界
脱炭素化で変わりゆく鉄道車両製造
~国内市場は堅調、
輸出向けも大きく伸びる可能性~
国内向け鉄道車両の需要は
1500~1600両で推移
日本鉄道車輌工業会の「2021年度鉄道車両の生産動態と需要見通し」(2021年10月発表)によると、2021年度の生産両数(輸出向け含む)は1840両、2022年度は1622両と予測されています。2023~2025年度の中期予測では、毎年1740両前後で推移するとみられています。
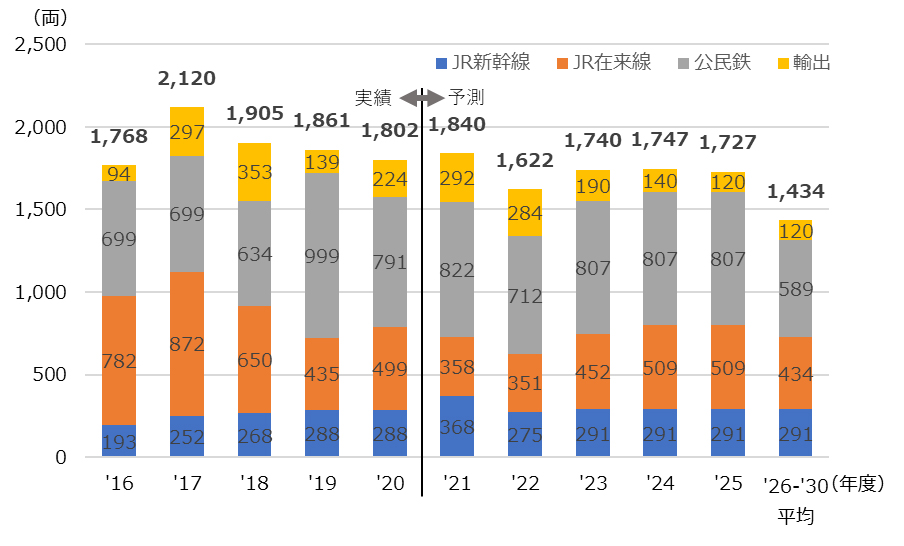
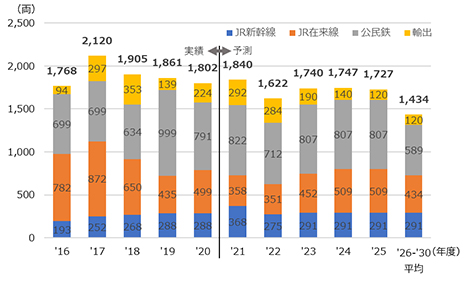
※出典:日本鉄道車輌工業会
「2021年度鉄道車両の生産動態と需要見通し」(2021年10月発表)
同工業会によると、日本国内には2021年4月1日現在、6万2747両の鉄道車両が在籍しており、2021年度の国内向け新造車両は1548両と予測されています。新幹線・地下鉄が増加した一方、JR在来線、関東・中部・関西・九州の大手民鉄は減少しました。2022年度は新幹線・地下鉄が減少に転じ、1338両と予測されています。
国内向けの中期見通しとしては、2023年度は1550両、2024年度は1607両、2025年度は1607両と予測。電車だけで2500両を超えたこともある高度成長期のような規模での生産は見込めませんが、1500~1600両程度の需要が望めるとしています。
コロナ禍により輸送需要の低迷が続き、2020年度以降は各鉄道事業者の経営状況が大きく悪化しました。その結果、新車の投入計画・設備投資計画の見直しや後ろ倒しが行われることも懸念されましたが、今のところ大きな計画見直しなどは発表されていません。
社会インフラとしての性格が強い鉄道車両は、中長期的な新線開通計画や車両更新計画に基づいて生産されるため、業績が悪化したからといってただちに設備投資計画が見直されるわけではありません。それよりも今は、時間帯に応じて変動する運賃を機動的に導入できる制度の導入や、災害対策・安全対策の名目で運賃・料金制度の見直しを行うといった方向で議論が進められています。
懸念されるのは、半導体不足です。すでに、ドアの開閉やブレーキを制御する機器などで使用する半導体の調達難により、鉄道車両の納入遅れが発生しています。この状況が長引けば、今後の車両の新造計画にも影響が広がるおそれがあり、予断を許しません。
国内の主要な鉄道車両メーカー
国内の代表的な鉄道車両メーカーとしては、日立製作所、川崎車両(旧・川崎重工業車両カンパニー)のほか、JR東海系の日本車輌製造、JR東日本系の総合車両製作所、近鉄グループでJR西日本との関係が深い近畿車輛の5社が挙げられます。この5社はいずれも新幹線車両を製造しており、JR在来線・公民鉄の特急車両・通勤車両も多く手がけていることから、日本の鉄道車両産業の主役と言えるでしょう。
このほかにも、「ゆりかもめ」のような新交通システムを得意とする三菱重工エンジニアリング、機関車を得意とする東芝インフラシステムズ、路面電車車両の国内トップメーカーであるアルナ車両といった鉄道車両メーカーが活躍しています。
鉄道車両のモノづくり
― 構体はステンレス製とアルミ合金製
鉄道車両を構成する製品には、「台車」「構体」「床下機器(電気機器・駆動装置など)」「空調機器」「内装」などがあり、「台車」以外は板金加工部品が多く用いられています。
「構体」は台枠・骨組・外板などで構成され、鉄道車両のボデーに相当する代表的な製品です。使用材料は、最初期は「木製」、その後は火災対策のため「鋼製」、腐食に強く軽量化が可能な「ステンレス製」、腐食に強いうえにさらなる軽量化が可能で成形性・塗装適性に優れる「アルミ合金製」が採用されてきました。現在は、ほとんどの鉄道車両が「ステンレス製」か「アルミ合金製」の構体を採用しており、コスト・耐久性・軽量性・成形性などのバランスによって使い分けられます。
ステンレス構体は、通勤車両や近郊型の車両で多く採用されています。腐食に強く剛性に優れるため外板を薄くすることができ、塗装工程を省略できます。アルミ構体と比べて低コストですが、複雑な形状への成形が難しく、塗装に向かないため、基本的にはシンプルな箱型の通勤車両に適しています。
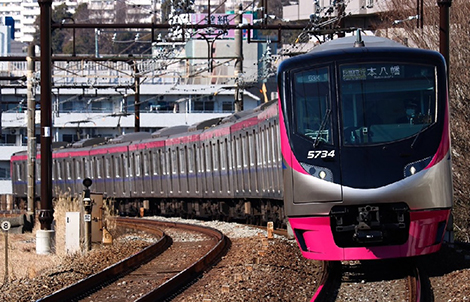
ステンレス構体を採用した京王電鉄の京王5000系電車(総合車両製作所製)
※Photo by 速水国府 (2019) / CC BY-SA 4.0
アルミ構体は、新幹線や個性的な外観の特急車両、一部通勤車両に採用されています。腐食に強いうえにステンレス以上の軽量化が可能で、リサイクル性(融点が低く省電力で再生可能)、加工性、気密性、塗装適性に優れているのが特長です。製造コストはステンレス構体よりも高くなりますが、軽量性や空気抵抗を低減するデザインが重視される高速鉄道、意匠性が重視される特急車両などに適しています。
材質によって大きく異なるのが接合方法です。ステンレス構体は、スポット溶接、レーザ溶接、MIG溶接、TIG溶接が用いられ、近年は外板のひずみやスポット溶接の圧痕が目立たないレーザ溶接の普及が進んでいます。アルミ構体は、MIG溶接、FSW(摩擦攪拌接合)、TIG溶接が用いられ、近年はアルミの弱点である熱影響を最小限に抑えられるFSWの普及が進んでいます。
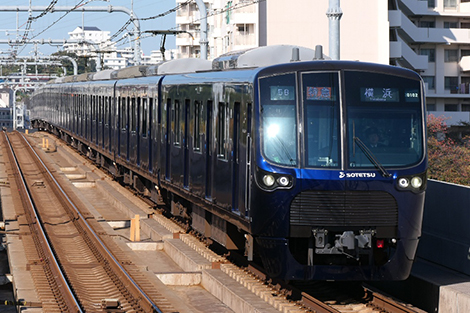
アルミ構体に塗装を施した相模鉄道の相鉄20000系電車(日立製作所製)
※Photo by MaedaAkihiko (2020) / CC BY-SA 4.0
「標準化」がテーマ
― 各社が製造プラットフォームを展開
鉄道車両のモノづくりは、ほかの産業分野と同様、「標準化」が大きなテーマになっています。
東海道新幹線の主力車両であるN700Sは、JR東海が開発し、日本車輌製造と日立製作所が製造しています。N700Sは搭載機器の小型軽量化により床下機器の配置を最適化した「標準車両」を採用しており、号車種別を従来の8種から4種に半減しました。これにより、基本設計を変更することなく、12両編成や8両編成に対応でき、山陽新幹線や九州新幹線での使用や海外輸出にも柔軟に対応できます。これまで編成両数を変更する場合は、新型車両の設計と同等の大規模な設計見直しが必要でしたが、「標準車両」の採用により、高品質な車両を低コストかつタイムリーに提供できるようになりました。
また、鉄道車両メーカー各社は、日立製作所の「A-train」(アルミ)、総合車両製作所の「sustina」(ステンレス)、川崎車両の「efACE」(ステンレス・アルミ)といった車両製造プラットフォームを持ち、「標準化」を進めています。
最近の動きとしては2021年11月、日本車輌製造が「第7回鉄道技術展」で、次世代プラットフォームの新ブランド「N-QUALIS」を発表しました。これまでは出入口の数や位置、強度や剛性など様々な要素があり、各鉄道事業者の要求仕様に合わせて個別に設計対応してきましたが、リードタイム短縮と品質向上を目的に、車両構造のプラットフォーム化を目指しています。
ステンレス製の構体ではスポット溶接での組み立てが基本となっていましたが、これをレーザ溶接とし、構造シミュレーションを用いて構造部材を効率よく配置することで、強度・剛性を向上させています。外板のひずみやスポット溶接の圧痕が少なくなり、美観性も向上させています。また、表面を平滑化し、構体シール箇所の削減なども図られています。
鉄道車両の脱炭素化
― 「電車」は省エネ化・再エネ化を推進
2050年のカーボンニュートラル実現へ向け、国内の鉄道産業にも脱炭素化の取り組みが求められています。
鉄道はもともと環境負荷の低い輸送手段であり、国土交通省によると、輸送量あたりのCO2排出量は、旅客で自家用乗用車の1/8、貨物で営業用貨物車の1/13となっています。特に電化路線を走行する「電車」は、軽量化に加え、LED照明、高効率モーター、高効率インバーター、次世代SiCパワー半導体、回生ブレーキなどの最新技術が採用され、脱炭素・省エネの観点ではすでに高い水準に到達しています。
「電車」は今後、以下が主なテーマとなります。
- ① 省エネ性能が高い最新技術の普及率を高める
- ② 回生ブレーキで得られた電力を貯蔵する蓄電池を車両側・地上側の双方に増設して「エネルギー回生率」を高める
- ③ 調達電力の再エネ化
特に③調達電力の再エネ化については、鉄道事業者の場合、駅構内・駅屋根・法面(斜面)・高架構造物・廃線跡地・鉄道林などを抱負に持っているため、そうした場所を活用して、太陽光発電(特に次世代のペロブスカイト太陽電池)や陸上風力発電の設置拡大が検討されていくことになります。
非電化路線の脱炭素化が課題に
非電化区間の脱炭素化も課題です。世界的に見て電化率が高い日本でも、全国の電化率は2/3程度。残り1/3の非電化路線ではディーゼル車両をはじめとする「気動車」が運行しており、排気ガスや温室効果ガスの排出削減が課題となっています。
全路線・全区間の電化ができれば話は早いのですが、巨額のイニシャルコストが必要になるうえ、電化を果たした後のメンテナンスコストも高額になり、利用者数が少ない地方路線では現実的ではありません。トンネルや橋梁など地形的要因によって架線を張ることが難しい区間もあります。
そのため、車両に蓄電池を搭載し、ディーゼル発電機と蓄電池の電力により走行する「ディーゼルハイブリッド車両」や、電化区間で蓄電した電力により非電化区間を走行する「蓄電池車両」が開発され、これまで全国に約140両が投入されています。
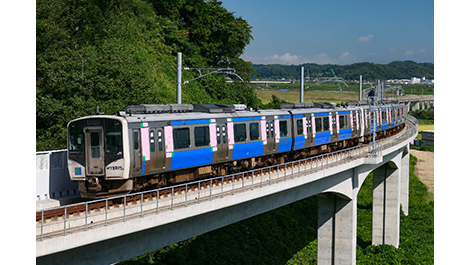
JR仙石東北ラインを走行する
「ディーゼルハイブリッド車両」(総合車両製作所製)
※Photo by MaedaAkihiko (2021) / CC BY-SA 4.0
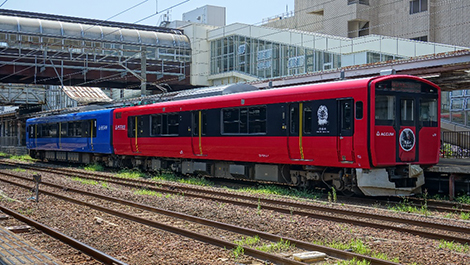
JR男鹿線を走行する「蓄電池車両」(日立製作所製)
※Photo by 掬茶 (2019) / CC BY-SA 4.0
次世代技術として注目されているのは、「バイオディーゼル燃料」などのバイオ燃料、ディーゼルなどのエンジンで発電した電力でモーターを駆動させる「電気式気動車」、そしてグリーン水素への転換を前提とした「燃料電池鉄道車両」です。
2022年2月には、JR東日本・日立製作所・トヨタ自動車が共同開発した水素を燃料とする燃料電池と蓄電池を電源とするハイブリッド試験車・FV-E991系「HYBARI」(ひばり)が発表されました。車両の製造は総合車両製作所が行い、燃料電池装置はトヨタ自動車が、主回路用蓄電池や電力変換装置を含むハイプリッド駆動システムは日立製作所が開発しました。
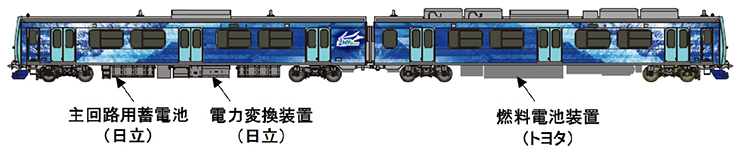
「HYBARI」の車両構成
(JR東日本のプレスリリースより)
水素を燃料とした車両はドイツですでに実用化されていますが、JR東日本によると、コンパクトな設計が必要となる狭軌車両としては世界初ということです。2022年3月下旬から南武線や鶴見線で走行試験を始め、東北地方の非電化区間などへの投入を視野に、2030年度をめどとして実用化を目指します。
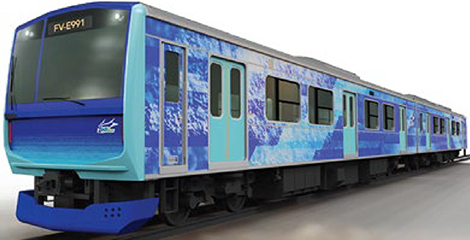
ハイブリッド試験車・FV-E991系「HYBARI」の外観イメージ
(JR東日本のプレスリリースより)
人口減少とモータリゼーションの進展により、地方路線の利用者数は減少の一途をたどっています。そうした中、JR東日本は経営体質を抜本的に強化する具体策として、「電化区間の架線や変電設備などを撤去(非電化とする)」「単線化などにより、線路や信号設備などを撤去」を挙げています。これは、電化路線のメンテナンスコストの負担の大きさを端的に示しています。カーボンニュートラルへの対応が求められる時代、非電化路線を増やす動きに比例して、「気動車」の脱炭素化の動きは活発化していくとみられています。
国内市場は堅調、輸出向けも
大きく伸びる可能性
社会インフラとしての性格が強い鉄道車両は、国内市場に限っても堅調な需要が続くと期待されます。また、世界的な脱炭素化の流れを受けて、輸出向けの生産も大きく伸びる可能性があります。
欧州鉄道産業連盟(UNIFE)によると、世界の鉄道市場(軌道、車両、信号・システム、運行・保守など)は年間27兆円規模(2023~2025年の平均)で、2025年まで年率2.3%で成長すると予測されています。
アジア・新興国では経済・産業の発展にともない長距離輸送を実現する高速鉄道、都市部の鉄道網や新交通システムなどの整備計画が目白押しとなっています。欧米など先進国でも、環境負荷が小さく大量輸送を実現できる鉄道インフラがあらためて注目されています。
日本政府が受注獲得に力を入れてきた新興国の高速鉄道計画は不調が続いていますが、鉄道車両メーカーが単独または商社と一体となって海外案件を勝ち取るケースは引き続き好調です。近年では、日立製作所が英国で次世代高速鉄道の車両を受注し、川崎車両はニューヨーク地下鉄など米国の地下鉄車両で引き続き強みを発揮。三菱重工エンジニアリングはシンガポールやマカオで新交通システムを、東芝インフラシステムズはドイツでハイブリッド機関車を受注したと伝えられています。
もともと日本の鉄道車両メーカーは、高度な技術力、納期遵守、故障の少なさ、きめ細かい顧客対応などにより、海外市場でも高い評価を得ています。今後は世界的な脱炭素化の潮流の中で、最新の省エネ技術、軽量化技術、そして電気式気動車や燃料電池車両といった次世代車両の開発力がさらなるアドバンテージにつながることが期待されています。
記事:マシニスト出版