曲げ加工の不良を低減したい
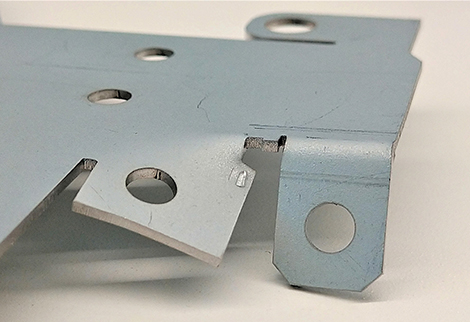
曲げ加工の現状
近年の製造業において、お客さまを取り巻く課題はますます深刻化しています。なかでも、曲げ加工は熟練した技能を必要とし、熟練技能者を育成するにも長い期間がかかります。追い打ちをかけるように、日本の高齢化率は2023年に29.1%と過去最高を記録すると同時に、生産年齢人口の減少も深刻です。技能をもった優秀な人材を新たに採用することは、年々難しくなっています。
深刻な人手不足
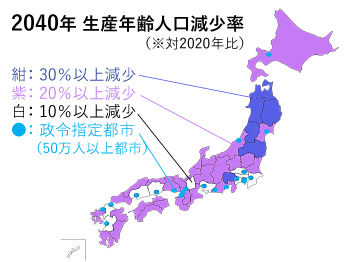
出典:国立社会保障・人口問題研究所の資料より作成
教育工数の負荷
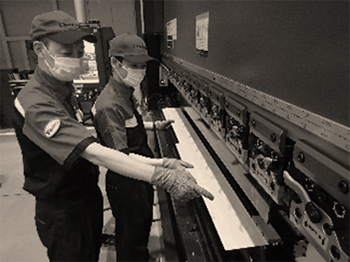
曲げ加工の課題
曲げ加工は、材料を設置後加工終了まで、機械任せでほぼ人手がかからないブランク加工と異なり、オペレーターが材料を手で持ち、バックゲージに突き当てながら加工を行うため、人手がかかることが特徴です。
この突き当て作業は、曲げ位置に直接影響するため、製品の品質を左右する重要な工程です。技能者が行うことが望ましい作業ですが、繁忙期や人手不足の現場では、思わぬ突き当てミスが発生し、加工不良につながってしまいます。
このような加工不良は、歩留まり率を低下させるため、恒常的な改善が望まれます。
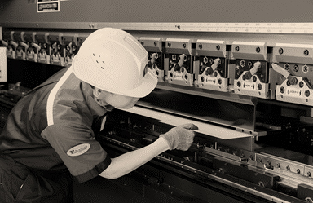
“曲げ不良”が発生してしまう主な原因
例1) 段取りや位置決めに時間がかかり、ミスが出やすい「異形状の製品」
●製品例:シンク
異形状の製品では、外形が曲げ線に対して平行でない場合が多くあります。
従来のバックゲージは、製品形状によっては適切に突き当てができない場合があり、特に異形状では加工が安定せず、その都度外形に合った治具の製作や、取り付け位置の調整に多くの段取り時間を要してしまいます。
あらかじめ曲げ線上に加工したケガキ線と、パンチ先端を合わせながら曲げる場合においても、一枚一枚の曲げ加工の位置合わせを行う工程に大変手間がかかるため、加工不良を誘発してしまいます。

シンクのイメージ
材 質 : SUS304
板 厚 : 1.0mm
製品寸法 : 465×134×315mm
部品点数 :1
加工時間 : 5分30秒
例2) 曲げ順、突き当て個所の間違えで、不良品が発生してしまう「複雑形状の製品」
●製品例:精密機器
複雑な製品形状の場合は曲げ数が多くなり、さらにどの順番で曲げるべきか、どこを突き当てるのか、材料の表/裏のどちらを上にして曲げるのかなどの判断に技能を要します。また、これらをひとつでも間違えると、正しい製品にはなりません。曲げ加工で不良品を出さないためには、熟練した技能と集中力が必要になります。
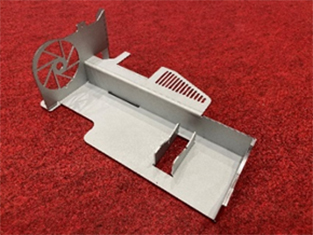
精密機器のイメージ
材 質 : SECC
板 厚 : 1.6mm
製品寸法 : 260×90×140mm
部品点数 :2
加工時間 : 1分19秒
これらのように、複雑な形状で難易度の高い曲げは、熟練した技能と高い集中力、そして高度な段取りが要求されます。
“曲げ不良”を低減する方法はある?
近年増えつつある製品の複雑化に伴い、曲げの順番や、突き当て個所などを間違えやすく、万が一 “曲げ不良”が起きると、再段取りの工数や材料などのコストがムダにかかることになり、結果、生産性の低下を招いてしまいます。
特に、熟練した技術を要する曲げ加工は、スキルに頼らない生産体制の構築が望まれます。