「生産スケジューラー」が
実現する超高効率生産!
中小製造業における
生産スケジュールの課題
近年、生産プロセスの“見える化”と“生産計画の作成”に特化した「生産スケジューラー」への注目度が急速に高まっています。
これまで中小製造業における生産スケジュールは、会社全体の受注状況や工場全体の生産状況を詳細に把握している役職者(工場長や製造部長)が大日程を作成し、朝礼・終礼で各課・各工程のリーダーがすり合わせを行い、ホワイトボードや紙、口頭で担当者レベルに落とし込むというのが一般的な手法でした。生産内容やメンバー構成にもよりますが、小規模な工場を中心に今でもこの手法は広く浸透し、有効に機能しています。
しかし近年は、熟練社員の引退と人手不足、業界再編に伴う企業規模の拡大が重なったことで、これまで現場の監督や生産計画を一手に担ってきた中核人材 — 「現場を把握できる社員」「計画を作成・管理できる社員」が不足しています。この傾向は、システム化が進んでいる大手メーカーよりも個人への依存度が高い中小製造業ほど強く見受けられ、深刻な課題となっています。
もちろん板金業界も例外ではなく、板金企業を対象にしたアンケート調査では、「課題となっている人材」という設問に対して「中堅リーダー(工程リーダー)」「現場監督者(工場長・現場責任者)」と回答する経営者が突出して多くなっています。
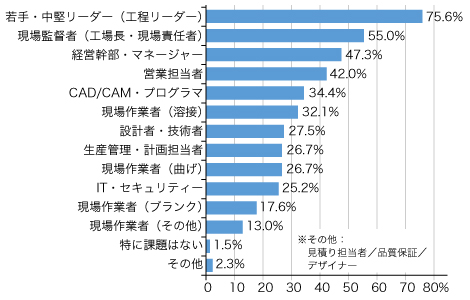
※出典:マシニスト出版
「Sheetmetalましん&そふと」2021年1月号
さらに、多品種少量生産・変種変量生産へのシフトが進み、特急・割り込み案件や計画変更(リスケ)が頻発するようになったことで、生産状況はますます複雑になっています。そのうえ「働き方改革」による時間外労働の上限規制により、担当者ごとの負荷の管理も必要になり、よりきめ細やかな把握・計画が求められています。
「生産現場の状況が見えない」「最適な生産計画が立てられない」「生産計画の難易度が上がっている」 — この3つが工場を運営するうえで大きな課題となっています。
リソースの能力を最大限に引き出す
「生産スケジューラー」
そこで注目されるようになったのが「生産スケジューラー」です。生産スケジューラーの一義的な役割は、AI・IoTを含むテクノロジーを駆使して最適な生産計画を策定し、工程・設備・人材といったリソースの能力を最大限に引き出すことです。
しかし、「生産スケジューラー」は「計画」の機能だけでなく、「進捗」「実績」の管理ツールを統合している(少なくとも連携している)のが一般的です。
「計画」は作成したら終わりというものではなく、常に「進捗」「実績」とセットで考えられます。計画を走らせた後は、リアルタイムで「進捗」を把握し、必要なら速やかに計画を修正しなければなりません。「計画」と「実績」が大きく乖離していれば、その理由を分析し、次の計画に反映させなければなりません。受注単価が適正かどうかにも直結するため、場合によっては見積りのコストテーブルに変更を加える必要もあります。
この「進捗」「実績」の管理の場面で、進歩が著しいIoT技術が生きることになります。
従来は、現場の作業者がPC端末やモバイル端末から実績情報を入力していましたが、現在は、対応している加工機から実績情報を自動取得し、リアルタイムにシステムに反映する技術が確立されています。
本来の「計画」の機能よりも、こうした「進捗・実績管理」の機能 — 特に加工機から実績情報を自動取得できる機能に期待して生産スケジューラーを導入する企業も目立ちます。むしろ今の時点では、難易度の高い「計画」は今後の課題としつつ、まずは「進捗」「実績」の管理からスタートして、生産プロセスの“見える化”を目指す企業の方が多く見受けられます。
板金加工業に特化した
生産スケジューラー「vLot Manager」
アマダの変種変量生産対応製造支援システム「vLot Manager」(ブイロット マネージャー)は、板金加工業に特化した生産スケジューラーです。
「vLot Manager」は、管理者向けのアプリケーション「vLot Planner」(ブイロット プランナー)と、作業者向けアプリケーション「vLot Navi」(ブイロット ナビ)で構成されています。
vLot Manager
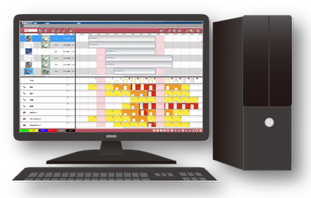
管理者向けのアプリケーション
vLot Planner
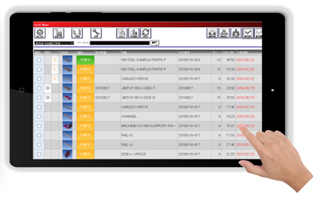
作業者向けアプリケーション
vLot Navi
パソコン上で動作する「vLot Planner」は、事務所の管理者が工程別・機械別・担当者別の負荷状況を見ながら柔軟な生産計画を策定できます。一方、主にモバイル端末で動作する「vLot Navi」には、「vLot Planner」で作成した生産計画に基づいて工程ごと・作業者ごとのジョブリストが表示され、自分が次に何をすべきかが一目でわかります。
進捗・実績情報は、アマダのNC端末のAMNC 3iまたはAMNCを搭載した加工機であれば、作業者の手間をかけることなく自動的に登録されます。それ以外の作業は、担当者が「vLot Navi」上で「着手」「完了」の情報を登録することになります。その情報は即時反映され、事務所の「 vLot Planner 」からリアルタイムに進捗状況を把握できます。
これらの機能により、受注情報の“見える化”(オーダーリスト)、全体スケジュールの“見える化”(ガントチャート)、仕事量の“見える化”(工程ごと・機械ごと・担当者ごとの負荷グラフ)を実現するとともに、柔軟できめ細やかな生産計画を策定できます。
ここからは、生産スケジューラー「vLot Manager 」を導入している板金企業3社の事例を紹介していきます。
柔軟な生産スケジュール・
負荷平準化に対応する
防水用長物鋼板やパブリック向けトイレパネルといった建築内外装部品を手がける葵ロール(株)(神奈川県伊勢原市、代表取締役:泉健二氏)は、「vLot Manager」本来の「計画」の機能を活用することで成果を挙げた企業です。
同社は「工場運営は“計画”がすべて。生産計画がしっかりしていないと、どれだけがんばって仕事をしても利益を出せない」(泉健二社長)という考えに基づき、以前から生産計画の充実に取り組んできました。
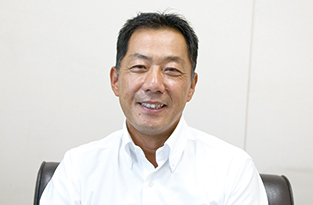
泉健二社長
以前は現場の作業者が実績工数を日報として提出し、それを「生産計画課」のメンバーが集計してST(標準作業時間)を割り出し、それをもとに営業の受注情報から生産計画を策定して、毎月の工数・負荷を管理してきました。
しかし、1カ月分の工数の総量は把握できても、週ごと、日ごと、設備ごと、担当者ごとに負荷は大きく変動します。計画担当者は、1カ月単位の大日程から1週間単位の中日程、1日単位の小日程へと落とし込んでいく過程で生産計画を調整し、負荷の平準化を行わなければなりません。しかし、こうした作業をExcelなどで行うには限界がありました。
泉社長は「1つの製品に対していくつもの子部品が付きますし、それぞれの部品が何工程にも分かれます。中日程・小日程へと落とし込むだけでも膨大な工数が必要で、調整の際にはすべての子部品、すべての工程を連動させなくてはなりません。ふたを開けてみると、2日後は残業6時間とか、とうてい成り立たない日程になってしまうこともありました」と語っています。
泉社長は、めまぐるしく状況が変化する板金工程を“見える化”するとともに、高精度な生産計画を効率よく策定できるツールとして「vLot Planner」の導入を決断しました。
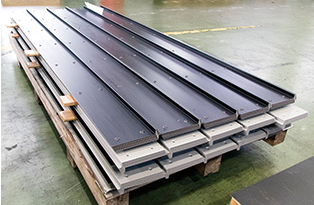
防水用長物鋼板(塩ビ被覆鋼板)
「vLot Planner」を導入してからは、1カ月ごと、週ごと、日ごと、設備ごと、担当者ごとの負荷の状況を細かく把握できるようになりました。計画を調整する際は、「この製品を後ろに動かした場合、どうなるか」といったシミュレーションが簡単にできるため、計画の精度が大幅に向上しました。突出した負荷があれば早い段階で把握でき、特急・割り込みが入ってもフレキシブルに対応できるようになりました。
泉社長は「以前は3人がかりで、オーダーの追加や計画調整に追われながら毎日残業・毎週休出という状況でしたが、現在は担当者が1.5人に半減、残業時間も軽減できました。
計画の調整も感覚的にできるため、経験の浅い担当者でもひとりで計画できるくらい簡単な作業になりました。組立に必要な部品が前工程から届かないといった“手待ち”もなくなり、ムダの削減、工場全体の生産性向上にもつながっています」と成果を語っています。
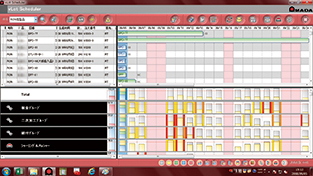
“vLot Planner”の画面
進捗状況とジョブリストの
リアルタイム管理
(株)たつみ(千葉県市川市、代表取締役:堀川義雄氏)は、「計画」よりも「進捗」をリアルタイムで管理するツールとして「vLot Manager」を活用しています。
同社は「モノづくりのコンビニエンスストア」をコンセプトに掲げ、得意先社数は200社を超えます。業種は建築・建設機械・産業機械など多岐にわたり、納期3日以内が80%以上、新規品が90%程度、ロットサイズは1~2個が大半という「超短納期・多品種少量生産」に対応しています。
同社のデジタル化・“見える化”を主導する谷雄人専務は「当社には生産管理システムがなく、これまではアナログな方法で曲げ工程だけを管理していました。事務所のホワイトボードを曜日で区切り、プログラマーが加工データを作成した時点で、得意先・納期・材質・板厚・特記事項を付箋紙に書いて、納期の曜日のところに貼り付けていました。10時・12時・15時・終業時に加工が完了した指示書が事務所に上がってきて、付箋紙を剥がします。直感的な目で見る管理という意味では効果的でしたが、さすがに対応しきれなくなってきました」と振り返ります。
生産拠点が3カ所に分散しているのも問題でした。
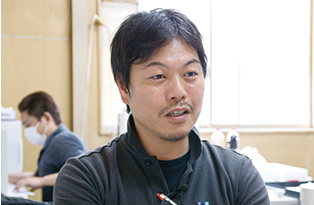
堀川義雄社長
「仕事量の増加にともない、進捗状況 — 加工がどこまで進んだのか、製品がどの工場にあるのか、まったくわからなくなりました。お客さまからの問い合わせも増え、そのたびに電話をしたり、現場を走り回ってモノ探しをしたりしなくてはなりませんでした」(谷専務)。
そこで、まずは「vLot Planner」をプログラマーの人数分(5台)導入し、付箋紙のかわりに、「vLot Planner」に得意先・製品名・数量・工程・納期などを登録。作業指示書と図面をセットにして現場へ生産手配をかけるようにしました。現場の作業者は、セットに含まれるすべての部品の加工が完了すると、現場のPC端末やタブレット端末の「vLot Navi」から消し込みを行います。その情報はリアルタイムに反映され、製品が今どこにあるか、事務所の「vLot Planner」ですぐに確認できるようになりました。

谷雄人専務
「プログラマーが「vLot Planner」に登録した時点で、各工程のジョブリストに反映されるため、作業者は作業指示書が届く前に、これからどんな仕事がくるか把握できます。船橋第2工場(レーザ専門工場)のオペレータは、最新のジョブリストをチェックしながら、夜間に自動運転で加工する仕事を考え、自動棚への材料段取りを行います。本社工場の曲げ・溶接作業者は、これから加工する製品が船橋第2工場を出荷したかどうかがわかり、事前に準備を進められます」(谷専務)。
堀川義雄社長は「究極的には、宅配便や宅配ピザのように、お客さまとも進捗情報を共有することで問い合わせを減らし、付加価値を高めたい」と意気込みを語っています。
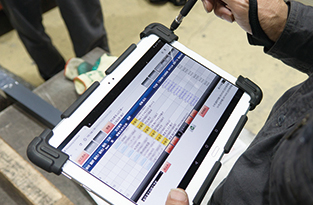
“vLot Navi”のタブレット端末
IoT技術で実績情報を加工機から自動取得
(株)北村鉄工所(京都府京都市、代表取締役:北村征志氏)は、加工機から実績情報を自動で収拾し、生産状況の“見える化”を行うツールとして「vLot Manager」を活用しています。
同社は、コア技術である溶接技術と、部品製作・外注手配・市販品手配・組立配線までワンストップで対応できる強みを生かし、医療機器、製薬機械、防災関連、食品機械の得意先を集中的に新規開拓してきました。現在は「包装リーク検出装置」や「米飯加工機械」といった自社ブランド製品も展開しています。
北村征志社長は「事業拡大にともなって、ここ4~5年の間に、従業員数が35名から45名に増えました。たかだか10名ですが、35名と45名では劇的にちがいました。一人ひとりの動きがまったく見えなくなり、ロスが増えるばかりで収拾がつかなくなりました」と語っています。
「もっと風通しを良くして透明度を高めていく必要がある — そのためにアマダの『V-factory』のようなIoTサービスを使って加工機から細かい生産実績データを吸い上げ、生産管理システムと連携させて、リアルタイムに“見える化”する仕組みをつくりたいと考えました」(北村社長)。
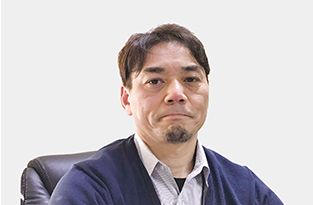
北村征志社長
同社では社内のSEが独自開発した生産管理システムを運用しており、それとアマダの「V-factory Connecting BOX」が収集する各加工機の稼働データをつなぎ込むために「vLot Manager」を導入したかたちです。また、「vLot Manager」の導入に先立ち、生産管理システムを改修して登録されている生産工程を細分化し、よりきめ細やかな“見える化”を目指しました。
「それまでは、製品が“できているか”“できていないか”くらいのレベルでしかわかりませんでしたが、「vLot Manager」を導入してからは、どのオーダーのどのパーツがどの工程まで進捗しているか、リアルタイムで把握できるようになりました」(北村社長)。
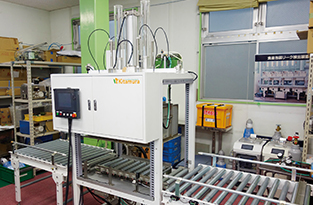
包装リーク検出装置
「収集したデータを分析すれば、現場に指示をする際の根拠になりますし、ロスや異常値の原因究明にも役立てられます。実際、それまでは当たり前と思っていたのですが、特定の工程の稼働率が極端に低いことがわかり、改善に取り組むことができました。生産プロセスと課題の“見える化”を実現できる「vLot Manager」は、経営ツールとして非常に有効だと思います」と北村社長は評価しています。
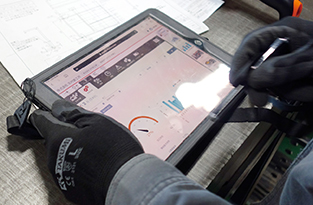
“vLot Navi”のタブレット端末
生産プロセスの“見える化”により生産性を高める
ここで紹介した3社は、業種・業態・生産内容・保有設備などすべてが異なるうえ、生産スケジューラー「vLot Manager」に期待する機能は、「計画」「進捗実績管理」「加工機からの実績情報の自動取得」と様々でした。
その一方で、3社とも業容を拡大する過程で製造現場の実態が見えなくなり、十分にコントロールできない状態に陥っているという悩みは共通しており、生産プロセスの“見える化”による生産性向上を目指していました。
冒頭で挙げた経営環境の変化 — 多品種少量生産・変種変量生産へのシフトや人手不足、企業規模の拡大やIoT・AI技術の進化などは、これからもますます顕著になっていくと考えられます。これからの板金業界のトレンドとして、生産スケジューラーによる生産プロセスの“見える化”と柔軟な生産計画への対応は検討していく必要がありそうです。
記事:マシニスト出版