溶接後の仕上げ作業を軽減したい
板金加工において代表的な製品として挙げられるのが配電盤や機械カバーといった『箱物形状』の製品です。
一般的な製法は、ブランク材を4辺曲げし、各コーナー(角部)をアーク溶接で溶接を行い、その後溶接部をグラインダーにより仕上げるといった手順で製作されます。
ステンレス材を用いた製品の一部では、バフ研磨を行って表面を滑らかに仕上げることもあります。
加工課題
このような製品の製造工程において、ボトルネックとなりやすいのが溶接後の仕上げ工程です。
従来の溶接方法では、まず各角部の継手を仮溶接(点付け)し、その後本溶接を行っていきます。この仕上げ工程において下記のような課題が発生します。
1. 溶接後のひずみ取りに時間がかかる
アーク溶接では、比較的広い範囲に大きな熱量が加わるため、材料が熱で溶けて膨張した後、熱が引いて収縮し、熱ひずみを発生させてしまいます。
このひずみ取りは、寸法を図面公差内に収めるためには行う必要があり、経験とノウハウが必要な大変難しい作業です。
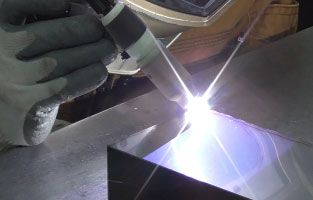
パルス電流による溶接
2. 溶接部の溶接ビード除去加工に時間がかかる
アーク溶接で溶接ひずみを軽減するため、パルス電流にて溶接した場合は溶接ビードの鱗目が残り焼け取り後も外観上目立ってしまいます。
この鱗目を除去するためには、仕上げ工程においてはグラインダーによる荒仕上げ、ペーパーディスクにて仕上げキズの除去、製品によってはさらにバフ研磨と段階を分けて仕上げていく必要があり、工数がかかります。
また均一に仕上げるには経験と技術が必要となります。
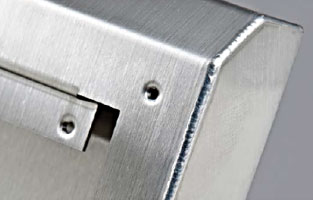
焼け取り後の鱗目

グラインダーによる荒仕上げ
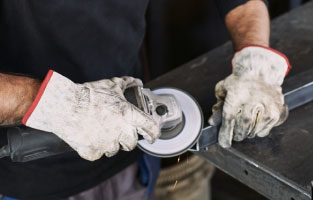
研磨仕上げした製品
この様に、溶接そのものにかかる工数より、溶接後の焼け取りやひずみ取り、仕上げなどの後工程の方が遥かに手間がかかっているということはよく見られる光景です。
しかも、これらの作業は、製品価値(高い品質)を大きく左右する重要な工程です。